GROWTH PROFILES AND ETHANOL PRODUCTION OF TWO YEAST STRAINS Kluyveromyces marxianus IFO-288 AND Kluyveromyces marxianus IFO-617 DURING FERMENTATION OF SOYBEAN PULP HYDROLYZATE SUBSTRATES
on
ARTICLE
GROWTH PROFILES AND ETHANOL PRODUCTION
OF TWO YEAST STRAINS
Kluyveromyces marxianus IFO-288 AND Kluyveromyces marxianus IFO-617 DURING FERMENTATION OF SOYBEAN PULP HYDROLYZATE SUBSTRATES
Kahar Muzakhar
Biology Department, The University of Jember, Jl. Kalimantan 37 Jember, Indonesia 68121 Email: [email protected]
ABSTRACT
Two yeast strains, K.marxianus IFO-288 and K.marxianus IFO-617, were observed to utilize carbon and nitrogen sources obtained from enzymatically hydrolyzed soybean pulp (hydrolyzate). Under aerobic condition where 1.5% hydrolyzate was used, the maximum biomass of the two yeast yield reached 30% with the protein contents of 47-53%. The two yeast strains also fermented the soybean pulp hydrolyzate and produced alcohol when anaerobic condition was set. The alcohol production efficiencies of the K. marxianus IFO-288 and K. marxianus IFO-617were 49% and 59.7%, respectively in the medium containing 1.5% hydrolyzate. These values were noticed to decrease for the two strains when the concentration of the hydrolyzate was increased. At the concentrations of 2.5% and 5% hydrolyzate for examples, the alcohol production efficiencies of the K.marxianus IFO-288 became 42.5% and 18.5%, respectively, while 45.6% and 20.8%, respectively were recorded in the medium inoculated with K. marxianus IFO-617. At 10% hydrolyzate concentration, none of the yeast strains grew or produced alcohol, indicating that some inhibitory substances in hydrolyzates were present in the fermentation medium.
Keywords: biomass, alcohol, fermentation, hydrolyzate
INTRODUCTION
Asignificant quantity of Soybean Pulp (SP) wastes containing hemicelluloses that is rich in carbohydrate and protein is disposed of from tofu production. The wastes were partially consumed as a traditional food. However, modernization and urbanization in lifestyle has reduced its status to that of mere industrial wastes (Ohno et al., 1996). These could be reasonably recovered and utilized by introducing microorganisms, such as fungi, so that the carbohydrate and the protein of the pulp could be degraded by the hydrolytic enzymes of the fungi into simpler compounds (sugars or amino acids) which could subsequently be utilized by yeast in the production of Single Cell Protein (SCP) or ethanol.
Previous study showed that a fungus, Aspergillus niger van Tieghem KF-267 was found to grow well on SP and secreted extracellular enzymes with the ability to liquefy the SP. Two enzymes had been purified and identified as an α-L-arabinofuranosidase (α-L-AFS) and an endo-β-D-1,4-galactanase (E-βGAL) (Muzakhar
et al., 1998). In this research, the possible use of SP as substrate in the production of ethanol and SCP is reported.
MATERIALS AND METHODS
Crude enzyme production
Five hundred grams of sterilized SP in a 5 liter flask was inoculated with Aspergillus niger v. Tieghem KF-267, incubated at 30oC for 4-5 days, harvested by adding 500 ml water containing 1% NaCl and 0.1% toluene (v/v), shaken at room temperature for 9 hours, and then centrifuged at 12000 rpm for 20 minutes. The supernatant as crude enzyme was then concentrated by ammonium sulphate at 70% saturation, dissolved and dialyzed against water for 3 days to remove the remaining ammonium sulphate, and stored at 4oC until needed for SP hydrolysis.
Degree of hydrolysis and total sugar content analysis
The degree of hydrolysis as reducing sugars was measured (Nelson, 1944; Somogy, 1952), and then calculated as follows:
Degreeof hydrolysis (%) =
Totalreducingsugarof SPhydrolyzate (w / v) *iqq% TotalSPsubstrate (w / v)
The total sugar content of SP-hydrolyzate was also measured by the phenol-sulphuric-acid method (Dubois et al., 1956).
Analysis of sugar composition of SP
Analysis for sugar composition of SP was done by using Hitachi Gas Chromatography (GC) as alditol acetates (Arai et al., 1978; Spiro, 1972). The GC was equipped with stainless steel column, 2 mm I.D. x 1.83 m, packed with 3% (w/w) ECNSS-M on Gas Chrom Q 100-120 Mesh (GL Sciences, Tokyo Japan). Nitrogen gas at the flow rate of 30 ml min-1 was used as carrier gas with the initial column temperature of 190oC for 5 minutes which was then gradually increased to 210oC at a rate of 1oC/min.
Thin layer chromatography of the hydrolyzate
The hydrolyzate was analyzed by using TLC in silica gel plate (Merck, silica gel 60 F254). A Mixture of 25% butanol : ethanol : chloroform : amonia (4:5:2:8) was used as solvent system and sulphuric acid containing 1% vanilin was employed for detection.
Preparation of SP-hydrolyzate medium for aerobic and anaerobic fermentation
Ten percent of dried SP was hydrolyzed using concentrated crude enzyme without any buffer condition and incubated at 37oC for 108 hours. The resulting hydrolyzate was harvested by centrifugation, concentrated, adjusted to pH 6, and diluted to appropriate concentration.
Growth and sugar assimilation of yeast
Three loop-full of K. marxianus IFO-0288 and K. marxianus IFO-0617 inocula were cultured aerobically in a 500-ml shake flasks using shaker set at 120 rpm and 30°C. One hundred ml refer as model medium was used, containing yeast-extract (0.3%), pepton (0.5%) and sugar (1.5%). Another medium used, contains only 1.5% SP-hydrolyzate. Growth or biomass (mg/l)
was observed by periodically measuring its absorbance at 660 nm every 12 hours.
The assimilated sugar and assimilation efficiency were calculated as follows:
Assimilated sugar (gr) = initial sugar (g) - remaining sugar (g)
( asimilated sugar (g) S
Assimilationefficiency (%) =I---------------------I
^ total sugar (g) )
*1QQ%
and the maximum yield of biomass were calculated as follows:
Maximumbiomass (g) Maximum yield of biomass (%) =-------------------* 1QQ%
Assimilated sugar (g)
Anaerobic fermentation and analysis of ethanol content
C6HiqO6 _C6H1Q°6____, C2H5OH + H2O
The yeast for anaerobic fermentation was prepared as follows; K. marxianus IFO-0288 and K. marxianus IFO-0617 were grown aerobically in 100 ml medium pH 6 in 500 ml shaker flasks, containing yeast-extract (0.3%), malt extract (0.3%), pepton (0.5%) and glucose (1%). The culture was incubated at 25°C under shaker set at 120 rpm for 24 hours, and active yeast cells were harvested by centrifugation at 3000 rpm for 10 minutes. The pellet (≈300 mg) was suspended in 4 ml sterilized water and used as a source inoculum in an anaerobic fermentation. Fermentation was conducted in 50 ml model and SP-hydrolyzate medium using mini fermenter. The medium was inoculated with 1 ml (≈75 mg) of source inoculum prepared above. During anaerobic fermentation, CO2 was released which caused gradual decrease in the weight of culture. The cultures were weighed and monitored for ethanol content at every 12 hours. The rate of released CO2 (mol) was equivalent to the rate of C2H5OH (mol) production.The ethanol concentration was also analysed using GC equipped with stainless column, 2 mm I.D. x 1 m, packed with Gaskuropack 54 mesh 80-100 (GL Sciences, Tokyo Japan).
Crude protein content analysis
The crude protein content was analyzed by using Shimadzu Gas Chromatograph GC
8A, equipped with Sumigraph NC 80. Fifteen milligrams of freeze-dried samples were ashed at 830oC and the released nitrogen was measured, using acetanilide as standard for calibration, to estimate crude protein content.
RESULTS AND DISCUSSION
The hydrolyzing experiment using crude enzyme with 10% substrate of dried-SP without any buffering condition resulted in 39% degree of hydrolysis after 108 hours incubation at 37°C. Nearly 50% degree of hydrolysis was obtained after 60 hours if the mixture condition was added with 100 mM acetate buffer pH 4 and incubated at 37°C. We found that the time delay in the degree of hydrolysis was due to delayed tendency of the crude enzyme to function at low pH condition, because its optimum pH is around 4, while its stability is in a pH range of 2.5 – 7.5. However, thereafter 72 hours the hydrolysis is still in progress and could presumably attain the same hydrolysis at very much later time. Whereas at 72 hours or as early as 60 hours with control the hydrolysis is almost complete with the same substrate. Furthermore, in previous result (Muzakharet al. 1998), we found that the α-L-AFS and E-βGAL enzymes also tend to function at low pH condition and exhibited maximum activity at pH 4.5 and 3.6 and retained nearly 100% activity in a pH range of 2-7 and 3-6 respectively.
SP-hydrolyzatewasrichinmonosaccharides but poor in oligosaccharides. The oligosaccharide concentration constituted less than 0.5% of the total sugar content. By the TLC analysis, it was found that the major hydrolysis products of dry-SP at the spots are monosaccharides, galactose, and arabinose spots, while oligosaccharides were not detected. GC analysis revealed that SP-hydrolyzate consisted of galactose (56.1%), arabinose (21.1%), glucose (12.1%), mannose (6.6%) and xylose (3.6%), while the minor components were fucose and rhamnose (Table 1). SP-hydrolyzate was also rich in crude protein up to nearly 18.5% on dry-basis which is sufficient
as a nitrogen source for fermentation material. The capability of crude enzyme to hydrolyze and produce mainly monosaccharide could be due to the fact that A. niger may not only secretes α-L-AFS and E-βGAL, but also a broad range of enzymes that could degrade the SP-hemicellulose simultaneously, that leads to an almost complete hydrolysis of carbohydrate.
Growth and aerobic fermentation (assimilation) using SP-hydrolyzate
The purpose of this observation was to determine assimilation ability and growth of biomass of K. marxianus IFO-288 and K. marxianus IFO-617 yeast strains by utilizing or exploiting the various sugars and protein found in SP-hydrolyzate as carbon and nitrogen sources, respectively. In the first step, a representative model medium, with sugar content compositions almost similar to SP-hydrolyzate (Table 1) was formulated.
Table 1. Sugar Composition of SP
Sugars |
Sugar composition per 10 g dried SP | ||
Acid hydrolys |
Enzymatic hydrolysis* | ||
is* SP-hydrolyzate4.9 g |
SP-residue 5.1g | ||
Total sugar (g) |
5.5 ~ 6 |
3.9 |
1.6 |
Sugar composition (%) : | |||
Rhamnose |
3.5 |
0.3 |
12 |
Fucose |
2.7 |
0.2 |
9.5 |
Arabinose |
21.1 |
21.1 |
18 |
Xylose |
11.7 |
3.6 |
24 |
Mannose |
10.9 |
6.6 |
13.5 |
Galactose |
40.3 |
56.1 |
15 |
Glucose |
9.8 |
12.1 |
8 |
*described in materials and methods
It was observed that K.marxianus IFO-288 and K.marxianus IFO-617 consumed the sugars and grew well in both model and SP-hydrolyzate medium. The growth or biomass concentrations of the two species were not significantly different between SP-hydrolyzate and model medium used. However, there was a difference in the time required for optimum growth. Both strains showed an optimal growth after 12-24 hours in SP-hydrolyzate medium, earlier than that in model medium where it took 48–60 hours of incubation. In addition to sugar as carbon source and protein as nitrogen source, SP-hydrolyzate may contain mineral and vitamins which are needed for growth when compared to the model medium. Furthermore, the reducing sugar in SP-
hydrolyzate medium was quickly assimilated which was indicated by a sharp decrease of reducing sugar profile within the first 12 hours, while in model medium it took 12-24 hours for both strains. These results suggest that SP-hydrolyzate is more readily exploited and a more suitable medium for both species when compared to the model medium.
Sugar assimilation analysis of each component showed that the yeast strains could easily assimilated glucose in all media used within a period of 0-24 hours. Galactose and mannose were also completely assimilated, while xylose and arabinose needed much longer time. However, in the model medium, after 72 hours of fermentation, xylose was not yet completely assimilated by K.marxianus IFO-288 and about 40% remained from initial concentration. Arabinose was also difficult to be assimilated by K.marxianus IFO-288 and K.marxianus IFO-617 in the model medium and also in SP-hydrolyzate medium inoculated with K.marxianus IFO-617 in which 50% of arabinose remained. These strains may lack the ability (weak, weak-slow or slow-seldom) to assimilate arabinose as a carbon source which is also found in others species of Kluyveromyces (Kreger, 1984). However, in SP-hydrolyzate medium inoculated with K. marxianus IFO-288, arabinose could be assimilated partially with only less than 10% remained.
In this study, both media gave the same maximum yield of biomass of almost 30% when
inoculated with the yeast strains. The protein content of the biomass in both strains was 47-53% on dry basis, which is not significantly different from that reported in previous research (about 50-55% for K. fragilis) (Kim et al., 1998). Overall result in this experiment proved that SP-hydrolyzate is a suitable medium as a source of carbon, nitrogen and vitamin for both strains for their growth, suggesting that SP-hydrolyzate showed a potential usage as a growth-medium for producing SCP.
Anaerobic fermentation
In the anaerobic fermentation of model medium inoculated with K. marxianus IFO-288 and K. marxianus IFO-617 (Fig. 1), CO2 gas was produced and it caused the weight of the culture to decrease accordingly. This evidence indicates that both strains could assimilate the sugar compounds of model medium under anaerobic conditions. Fig. 1 showed that the weight of model medium inoculated with K. marxianus IFO-617 decreased faster than the that inoculated with K. marxianus IFO-288. This suggests that, the fermentation and sugar consumption in the model medium inoculated by K. marxianus IFO-617 was faster than that in the model medium inoculated with K. marxianus IFO-288. The optimum period for fermentation was about 24 – 36 hours for the model medium inoculated with K. marxianus IFO-617 while 72 – 84 hours of incubation were required for the model medium inoculated with K. marxianus IFO-288. However,
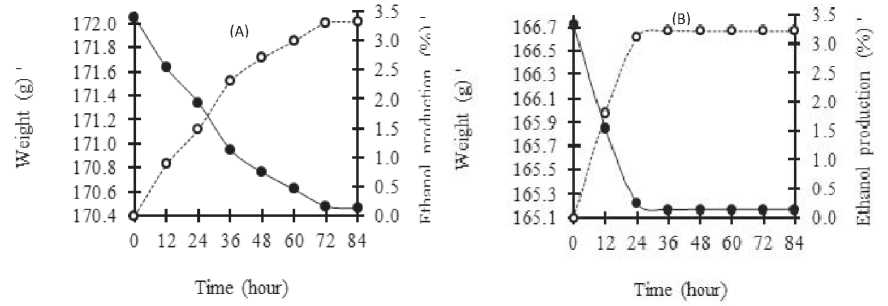
Fig.1. Profile of ethanol production in aerobic fermentation. Decreasing weight (•) of cultures and ethanol production (O) in fermentation using 10% model medium inoculated with K. marxianus IFO-288 (A) and K. marxianus IFO-617 (B).
Table 2.Ethanol Concentration and Ethanol Production Efficiency
Medium |
Yeast |
Sugar concentration (%) |
Analysis method of ethanol production | ||
Weight-Lost measurement (Winitial weight – Wfinal weight) |
Gas Chromatography measurement : Ethanol concentration (%) | ||||
Ethanol Concentration (%) |
Ethanol production efficiency (%) | ||||
Model |
K. marxianus 0288 |
10 |
3.2 |
80.9 |
3.1 |
K. marxianus 0617 |
10 |
3.3 |
73.5 |
3.3 | |
SP-hydrolyzate |
K. marxianus 0288 |
10 |
0 |
0 |
NA |
5 |
0.4 |
18.5 |
0.44 | ||
2.5 |
0.46 |
42.5 |
0.48 | ||
1.5 |
0.31 |
49.3 |
0.32 | ||
K. marxianus 0617 |
10 |
0 |
0 |
NA | |
5 |
0.42 |
20.8 |
0.44 | ||
2.5 |
0.46 |
45.6 |
0.53 | ||
1.5 |
0.36 |
59.7 |
0.39 |
NA: Not Analyzed
at the final stages of the experiment, both strains showed similar capability in the fermentation process, with ethanol production efficiencies of about 78.5% and 80.9% for K. marxianus IFO-288 and K. marxianus IFO-617, respectively, after 84 hours incubation.
In contrast, when 10% sugar from SP-hydrolyzate was used, both strains could not assimilate it and neither produced CO2 nor ethanol within 84 hours incubation. However, when 5% sugar of SP-hydrolyzate was used, both strains produced CO2 and ethanol although their efficiencies were low. Further, when using lower concentrations of 2.5% and 1.5% of SP-hydrolyzate, the concentration of ethanol production efficiency seemed to increase accordingly (Table 2). The highest alcohol production efficiency was achieved when 1.5% sugar SP-hydrolyzate was used in both fermentations with ethanol production efficiencies of 49.3% and 59.7% for K. marxianus IFO-288 and K. marxianus IFO-617, respectively. However, the alcohol production efficiency was still low compared to the model medium. Our result showed that the high sugar concentration of SP-hydrolyzate is not suitable for fermentation of these strains. As there is few literature available using SP as substrate for fermentation in ethanol production, we could not compare our study to another. We suggest that it could be the presence of inhibitors that may hinder the fermentation (Margaritis and Bajpai, 1982; Lark, 1997).
However, K. marxianus sp. has been reported to be capable of fermenting and producing ethanol using various sugars as carbon source (Larsson et al., 1999; Morikawa et al., 1985; Olsson and Hahn, 1999; Siso et al., 1996).
The ability of yeast to ferment sugars depends on various physicochemical parameters of substrates. Low production efficiency or the inability to ferment the substrate may be influenced by the presence inhibitory substances (e.g. acetic acid, hydroxymethyl furfural, o-hydroxybenzylalcohol, acetaldehyde, etc.) either in the substrate itself or produced during fermentation. Theamountandnatureofinhibiting compounds depends on the raw material, the prehydrolysis and hydrolysis procedures, and the length of circulation process. Based on this, the inability to ferment 10% SP-hydrolyzate maybe due to the presence of some inhibitory substances either in SP itself or produced during solid state fermentation by A. niger.
ACKNOWLEDGEMENT
The author wishes to thank the Directorate General Higher Education, Ministry of Culture and Education for financially supported this research.
REFERENCES
Arai M and Murao S. 1978. Characterization of oligosaccharides from an enzymatic hydrolyzate of red yeast cell walls by lytic enzyme. Agric. Biol. Chem. 42: 1651-1659.
Dubois M, Gilles KA, Hamilton JK, Rebers PA.and Smith F. 1956. Colorimetric method for determination of sugars and related substances.Anal. Chem. 28: 350-356.
Kim JK, Tak KT and Moon JH. 1998. A continuous fermentation of Kluyveromycesfragilis for the production of a highly nutrisious protein diet. Aquacultural Engineering 18: 41-49.
Kreger-Van R. 1984. The yeast a taxonomic study. Third revised and enlarged edition.Elsevier Science Publishers B. V., Amsterdam p. 224-252.
Margaritis A and Bajpai P. 1982. Continuous ethanol production from Jerusalem artichoke tubers, I. Use of free cells of Kluyveromycesmarxianus. Biotechnology
and Bioengineering 24: 1473-1482.
Lark N, Xia Y, Qin C, Gong CS and Tsao GT. 1997. Production of ethanol from recycled paper sludge using cellulase and yeast, Klyuveromycesmarxianus. Biomass and Bioenergy 12: 135-143.
Larsson S, Palmqvist E, Hahn-Hägerdal B, Tengborg C, Stenberg K, Zacchi G and Nilvebrant N O. 1999. The generation of fermentation inhibitors during dilute acid hydrolysis of softwood. Enzyme and Microbial Technology 24: 151-159.
Morikawa Y, Takasawa S, Masunaga I and Takayama K. 1985. Ethanol production from D-xylose and cellobiose by
Klyuveromycescellobiovorus. Biotechnology and BioEngineering 27: 509-513.
Muzakhar K, Hayashi H, Kawaguchi T., Sumitani J and Arai M. 1998. Purification and properties of α-L-arabinofuranosidase and endo-β-D-1,4-galactanase from
Aspergillusniger v. Tieghem KF-267 which Liquefied the SP. In K. Ohmiya et al. (ed.), Genetics, Biochemistry and Ecology of Cellulose Degradation. Proceeding of MIE BIOFORUM 98, Suzuka Japan. Uni Publisher Co., LTD. Tokyo Japan.134-143.
Ohno A, Ano T and Shoda M. 1996.Use of soybean curd residue, SP, for the solid state substrate in the production of a lipopeptide antibiotic, iturin A, by Bacillus subtilis NB22. Process Biochemistry 8: 801806
Olsson L and Hahn-Hägerdal-H B. 1999. Fermentationoflignicellulosichydrolysates for ethanol production. Enzyme
Nelson N. 1994 A photometric adaptation of the Somogy method for the determination of glucose. J. Biol. Chem. 153: 375-380.
Siso MIG, Ramil E, Cerdán ME and Freire-Picos MA. 1996. Respirofermentative metabolism in Klyuveromyceslactis: ethanol production and the crabtree effect. Enzyme and Microbial Technology 18: 585-591.
Somogy M. 1952. Notes on sugar determination. J. Biol. Chem. 195: 19-23.
Spiro G. 1972. Study of carbohydrates of glycoproteins, Methods in Enzymology. Academic Press, New York and London Vol.XXVIII. Ginsburg IV (ed.), Part B. p. 1-11.
udayana university biosciences and biotechnology forum • 77
Discussion and feedback