Penerapan Metode Six Sigma untuk Menurunkan Jumlah Defect pada Produksi Fillet Ikan Kakap Putih (Lates Calcarifer bloch)
on
JURNAL BETA (BIOSISTEM DAN TEKNIK PERTANIAN Program Studi Teknik Pertanian, Fakultas Teknologi Pertanian Universitas Udayana
http://ojs.unud.ac.id/index.php/beta
Volume 9, Nomor 1, bulan April, 2020
Penerapan Metode Six Sigma untuk Menurunkan Jumlah Defect pada Produksi Fillet Ikan Kakap Putih (Lates Calcarifer Bloch)
Application Six Sigma Method to Reduce the Number of Defects in the Production of White Snapper Fillets (Lates Calcarifer bloch)
Putu Ayu Aripradnyani, I Wayan Widia*, I Gusti Ketut Arya Arthawan.
Program Studi Teknik Pertanian dan Biosistem, Fakultas Teknologi Pertanian Universitas Udayana, Badung, Bali, Indonesia
Email: wayanwidia@unud.ac.id
Abstrak
Setiap perusahaan seyogyanya berupaya memperkecil resiko kegagalan dalam berproduksi. Tingginya persentase produk cacat dalam setiap siklus produksi selain berimplikasi terhadap menurunkan kepercayaan konsumen juga menaikkan biaya produksi sehingga berakibat menurunkan daya saing produk di pasar. Tujuan penelitian ini adalah mengidentifikasi faktor utama penyebab cacat pada produk dan menemukan bentuk perbaikan proses dan atau manajemen yang dapat dilakukan untuk mengurangi jumlah produk cacat pada proses produksi fillet ikan kakap putih kualitas ekspor pada salah satu perusahaan pengolahahan ikan di Bali menggunakan metode six sigma. Penelitian ini mencakup empat tahapan implementasi six sigma yaitu DMAI (Define, Measure, Analyze, dan Improve) yang melibatkan pihak manajemen dan karyawan perusahaan. Hasil penelitian menunjukkan bahwa teridentifikasi dua faktor kritis penyebab utama defect fillet ikan kakap putih, yaitu daging pecah/lembek dan berbau, dan pemberian gas CO yang kurang merata. Karakteristik kinerja yang dicapai oleh perusahaan saat ini dicirikan oleh angka DPU (Defect per Unit) sebesar 0,09, DPO (Defect per Opportunities) sebesar 0.045, DPMO (Defect per Million Opportunities) sebesar 45,463 yang setara dengan kinerja pada level 3,125-Sigma sehinga tergolong dalam kategori tingkat kinerja rata-rata industri. Perusahaan berpotensi meraih peningkatan kinerja hingga pada level 4,000-Sigma sepanjang bersedia melakukan sejumlah perbaikan secara berkesinambungan dalam manangani baik terhadap pengawasan mutu bahan baku ikan maupun ketidaksempurnaan pemberiaan gas CO pada produk. Dengan penerapan metode six sigma, maka penyebab utama kegagalan dapat diidentifikasi dan mendapat rekomendasi perbaikan dalam upaya meningkatkan kinerja proses perusahaan.
Kata Kunci: Fillet ikan, produk cacat, six sigma, pengendalian mutu, daya saing produk.
Abstract
Every company should try to minimize the risk of failure in production. The high percentage of defective products in each production cycle has implications not only reducing consumer confidence but also increasing production costs, which results in lower product competitiveness in the market. The objective of this study was to identify the main factors causing defects in the product and to find how can of process improvement and or management that can be done to reduce the number of defective products in the export quality white snapper fillet production process at a fish processing company in Bali using the Six-Sigma method. This research consisted of Six-Sigma implementation stages, namely DMAI (Define, Measure, Analyze, and Improve) which involved management and company employees. The results showed that two critical factors were identified as the main causes of white snapper fillet defect, namely broken/mushy and smelly meat, and uneven application of CO gas. The performance characteristics achieved by the company are currently characterized by a DPU (Defect per Unit) number of 0.09, DPO (Defect per Opportunities) of 0.045, DPMO (Defect per Million Opportunities) of 45.463 which is equivalent to performance at the 3,125-Sigma level so that belongs to the category of industry average performance level. The company has the potential to achieve an increase in performance up to the 4,000-Sigma level as long as it is willing to make a number of continuous improvements in handling both the quality control of fish raw materials and imperfections in the supply of CO gas in the product. With application of the six sigma method, the main causes of failure can be identified and get recommendations for improvements in an effort to improve the company’s process performance.
Keywords: Fish fillets, defect products, six-sigma, quality control, product competitiveness.
PENDAHULUAN
Fillet ikan kakap putih (Lates Calcarifer bloch) merupakan salah satu produk penting yang diproduksi oleh perusahaan pengolahan ikan di Bali. Fillet ikan yang dibuat dari ikan kakap putih atau disebut juga barramundi memiliki beberapa keunggulan diantaranya mempunyai kandungan protein 17-23% dengan profil asam amino sebanyak 9 jenis asam amino esensial (treonin, valin, fenilanin, leusin, metionin, lisin, isoleusin, arginine dan histidine) serta sejumlah asam amino nonesensial seperti asparat, glutama, serin, alanine, firosin, prolin dan glisin (Nurjanah et al., 2014). Fillet ikan utamanya produk kakap putih merupakan salah satu bahan makanan yang mudah sekali mengalami perubahan mutu (Try et al., 2018).
Tahapan pembuatan fillet ikan kakap putih secara garis besar terdapat beberapa proses yang dilalui seperti penerimaan bahan baku, penyisikan, pemfilletan hingga pengepakan (Sedana et al., 2015). Dalam proses produksi tersebut, sering dijumpai penyimpangan-penyimpangan berupa kesalahan dalam proses produksi fillet ikan yang menyebabkan defect minor maupun defect major pada produk (Farmayanti & Dinarwan, 2006). Faktor-faktor dari penyebab defect dapat terjadi akibat kondisi material yang tidak baik, mesin yang digunakan tidak layak, minimnya sumber daya manusia dan faktor lainnya. Oleh karena itu diperlukannya suatu serangkaian pengamatan/observasi untuk menentukan faktor dominan yang menyebabkan produk defect dan dilakukan suatu analisa dalam melakukan proses perbaikan.
Banyak metode dan atau teknik manajemen yang telah dikembangkan untuk membantu perusahaan dalam upaya meningkatkan kinerjanya. Metode ini merujuk pada falsafah Pengelolaan Mutu Menyeluruh (Total Quality Manajemen, TQM) menggunakan model Peningkatan Berkelanjutan (Continues Improvement, CI). Beberapa metode yang umum diaplikasikan di perusahaan untuk meningkatkan kinerja prosesnya yaitu diantaranya metode Kaizen, metode Business Process Reengineering (BPR), metode Failure Mode Effect Analyzis (FMEA), metode Quality Function Deployment (QFD), dan metode Lean-Tinking (Latief & Utami, 2010). Masing-masing metode memiliki keunggulan di satu sisi dan pada sisi lainnya juga memiliki beberapa kelemahan, salah satunya belum mampu membuktikan performance-nya dalam meningkatkan kualitas produk/perusahaan secara dramatis hingga mencapai tingkat kegagalan nol (zero defect) (Wahyani et al., 2010). Metode six sigma memiliki visi dalam meningkatkan kualitas hingga memenuhi target 3,4 kegagalan per satu juta kesempatan (DPMO) pada setiap hasil akhir produk
(Widiyawati & Assyahlafi, 2017). Penerapan metode six sigma berfokus pada cacat dan variasi, dimulai dengan mengidentifikasi unsur– unsur kritis terhadap kualitas yang dikenal dengan CTQ (Critical to Quality) dari suatu proses (Emilasari & Vanany, 2007). CTQ (Critical to Quality) merupakan hal yang perlu didefinisikan berdasarkan masukkan dari pelanggan terhadap kualitas yang diinginkan terhadap produk (Caesaron et al., 2015). Langkah sistematis dalam six sigma dikenal dengan metode DMAIC (Define, Measure, Analyze, Improve, Control). Benefit yang diberikan dengan menerapkan metode ini dapat mengetahui penyebab utama cacat pada produk, mengubah pola kerja suatu manajemen, mempererat hubungan antar karyawan sehingga dapat diterapkan pada berbagai level di perusahaan dimulai dari level strategis hingga pada level operasional (Soemohadiwidjojo, 2017).
Sebagai salah satu perusahaan pengolahan fillet ikan kakap putih beku atau segar, PT. I Am Be U Mina Utama telah meraih berbagai rekognisi dalam hal manajemen mutu yang bertaraf internasional seperti sertifikasi HACCP, BRC (British Retail Concorcium), sertifikasi ISO 22000:2005, dan beberapa sertifikasi mutu bertaraf nasional. Perusahaan ini memiliki anak perusahaan dengan nama PT. Bali Barramundi yang membudidayakan ikan kakap putih sebagai bahan baku dalam pengolahan ikan. Dengan adanya pembudidayaan ikan tersebut, maka produksi fillet ikan kakap putih dapat terpenuhi setiap minggunya.
Sebagai salah satu metodologi dasar dalam meningkatkan kinerja proses perusahaan, metode six sigma dicoba diterapkan pada PT. I Am Be U Mina Utama. Adapun tujuan dari penelitian ini adalah dapat mengidentifikasi faktor utama penyebab cacat pada produk dan menemukan bentuk perbaikan proses dan atau manajemen yang dapat dilakukan untuk mengurangi jumlah produk cacat pada proses produksi fillet ikan kakap putih kualitas ekspor pada salah satu perusahaan pengolahahan ikan di Bali menggunakan metode six sigma.
METODE
Tempat dan Waktu Penelitian
Penelitian ini dilaksanakan di Stasiun Proses Pembuatan Produk Fillet Ikan Kakap Putih di PT I Am Be U Mina Utama, Jalan By Pass Ngurah Rai No. 17, Pesanggaran, Denpasar, Bali dan pada Laboratorium Sistem Manajemen Keteknikan Pertanian, Fakultas Teknologi Pertanian, Universitas Udayana, Kampus Sudirman. Pelaksanaan penelitian ini dilakukan sejak akhir Bulan Desember 2019 sampai dengan Bulan Maret 2020.
Jenis Data
Data yang digunakan adalah data primer dan data sekunder. Data primer yakni jumlah produk defect minor pada produk fillet ikan kakap putih dan data berdasarkan wawancara dengan pihak karyawan yang terlibat pada permasalahan yang terjadi. Sedangkan data sekunder didapat berdasarkan studi literatur oleh peneliti lain serta data-data sekunder perusahaan yang menunjang lainnya.
Variabel Penelitian
Variabel yang diamati dalam penelitian ini meliputi jumlah produksi mingguan fillet ikan kakap putih, jumlah produk cacat (defect), klasifikasi kecacatan produk, karakteristik diagram SIPOC perusahaan, diagram alir proses produksi fillet ikan kakap putih, deskripsi tugas dan tanggung jawab karyawan, dan program HACCP perusahaan.
Metode Pengumpulan Data
Metode pengumpulan data yang digunakan adalah metode observasi, dan metode wawancara mendalam (depth-interview). Seluruh data primer dikumpulkan melalui pengamatan secara langsung di perusahaan. Proses validasi data dilakukan dengan cara melakukan konfirmasi silang antar divisi kerja dan konfirmasi silang antar bawahan dan atasan langsung karyawan.
Analisis Data
Analisis data yang dilakukan menggunakan metode Six Sigma yakni tahapan proses DMAI (define-measure-analyze-improve). Adapun analisis data yang dilakukan meliputi analisis data kuantitatif dan analisis data kualitatif. Analisis data kuantitatif meliputi perhitungan tingkat keberhasilan produksi, perhitungan jumlah penyebab dominan defect menggunakan metode NGT (Nominal Group Technique), penentuan urutan prioritas menggunakan Digaram Pareto (Pareto Chart), perhitungan angka DPMO (Defect per Million Opportunities), dan perhitungan kinerja Sigma perusahaan. Analisis data kualitatif penelitian dilakuan meliputi kajian terhadap proses bisnis perusahaan menggunakan Diagram SIPOC (Supplier-Input-Process-OutputCustomer), kajian penyebab produk cacat menggunakan Diagram Tulang Ikan (Fishbone Diagram), kajian terhadap penyebab kegagalan dalam menjalankan proses menggunakan alat analisis FMEA (Failure Mode and Effect Analysis), sedangkan kajian untuk menghasilkan rekomendasi untuk perbaikan menggunakan Teknik 5W+1H terdiri dari what (apa?), why (mengapa?), where (dimana?), when (kapan?), who (siapa?) dan how (bagaimana?) yang digunakan dalam memecahkan masalah untuk perbaikan (Pangaribuan & Handayani, 2019).
HASIL DAN PEMBAHASAN
Kinerja Proses Produksi Fillet Ikan Kakap Putih di PT. I Am Be U Mina Utama
PT. I Am Be U Mina Utama merupakan salah satu pemasok ikan segar dan olahan ikan segar kualitas kelas hotel dan ekspor di Bali, salah satu produknya adalah fillet ikan kakap putih. Perusahaan ini telah bersertifikat HACCP (Hazard Analysis Critical Control Point), ISO 22000 dan telah menerapkan syarat dasar GMP (Good Manufacturing Practices) serta SSOP (Sanitasi Standar Operasional Prosedur). Perusahaan ini memiliki 64 jumlah karyawan dengan menduduki jabatan masing-masing sesuai struktur organisasi yang berlaku. Berdasarkan hasil observasi, tingkat keberhasilan produksi perusahaan selama periode penelitian dapat dilihat pada tabel 1.
Berdasarkan tabel 1, rata-rata produksi fillet ikan kakap putih mencapai 2829 per minggu dengan jumlah produk defect rata-rata mencapai 271,6. Hal tersebut dapat diasumsikan bahwa kondisi defect minor pada produk fillet ikan kakap putih beragam/bervariasi dilihat dari hasil standar deviasi jumlah produk defect. Adapun tingkat keberhasilan produksi terendah terjadi pada minggu ke-IV Bulan Desember 2019, setelah diidentifikasi hal tersebut dikarenakan penghujung akhir tahun sehingga produk telah dikirim sebelum akhir Bulan Desember dan stock material yang menurun akibat ‘musim barat’ yang menandakan tingkat panen ikan di laut lepas yang sedikit. Sedangkan tingkat keberhasilan proses produksi yang paling tinggi terjadi pada minggu ke-II Bulan Januari 2020, hal tersebut dikarenakan panen yang meningkat setelah pergantian tahun dan produksi ikan budidaya semakin meningkat.
Tabel 1. Jumlah dan tingkat keberhasilan produksi mingguan fillet ikan kakap putih di PT. I Am Be U Mina Utama
Bulan |
Periode |
Produksi Fillet Ikan Kakap Putih |
Tingkat kesempurnaan proses (%) | |
Jumlah produksi (unit) |
Jumlah produk defect (unit) | |||
(a) |
(b) |
(c) |
(d) |
(e) = [(c)-(d)]/(c) x 100 |
Desember 2019 |
Minggu ke- IV |
334 |
90 |
73,0 |
Minggu ke- I |
1198 |
150 |
87,5 | |
Januari 2020 |
Minggu ke- II |
4301 |
220 |
94,9 |
Minggu ke- III |
4758 |
378 |
92,1 | |
Minggu ke- IV |
5851 |
675 |
88,5 | |
Minggu ke- I |
1837 |
183 |
90,0 | |
Februari 2020 |
Minggu ke- II |
2388 |
289 |
87,9 |
Minggu ke- III |
1224 |
201 |
83,6 | |
Minggu ke- IV |
3570 |
258 |
92,8 | |
Rata-rata mingguan |
2829 |
271,6 |
87,8 | |
Standar deviasi |
1877,8 |
172,4 |
6,5 |
Faktor Kritis Penentu Cacat pada Produk Fillet Ikan Kakap Putih
Dalam tahapan DMAIC, penentuan faktor kritis yang menyebabkan defect pada produk disebut tahap define. Alat yang digunakan dalam menentukan faktor kritis penyebab defect adalah diagram SIPOC (Supplier-Input-Process-Output-Customer) dan NGT (Nominal Group Technique). Diagram SIPOC menggambarkan alur proses produksi dimana dapat terjadi penyimpangan proses yang menyebabkan produk defect. NGT (Nominal Group Technique) digunakan sebagai alat pengambil keputusan berdasarkan sumbang saran oleh beberapa anggota tim yang terlibat (Rohmatulloh et al., 2017). Penyebab dominan defect minor berjumlah enam yang disepakati bersama tim berdasarkan kemunculan defect ringan akan tetapi memiliki pengaruh besar terhadap output produk. Gambar 1 menunjukkan Diagram SIPOC pada proses produksi fillet ikan kakap putih dan tabel 2 menunjukkan NGT (Nominal Group Technique).
Berdasarkan tabel 2, nilai NGT = (1/2 N +1) x jumlah anggota tim = ((1/2 x 6) + 1) x 5 = 20 dengan N merupakan penyebab dominan defect fillet ikan kakap putih, maka penyebab dominan dengan nilai NGT>20 dipilih sebagai faktor kritis penyebab utama defect fillet ikan kakap putih yakni (1) daging pecah/lembek dan berbau, dan (2) pemberian gas CO yang kurang merata.
Kondisi penumpukkan pada ikan segar dapat mempengaruhi kualitas daging. Menurut Zulkarnain et al (2013) penangkapan dan peletakkan ikan dalam jumlah banyak yang memungkinkan ikan
bertumpuk/saling berhimpitan dapat mengakibatkan memar dan luka atau bahkan menyebabkan ikan menjadi rusak secara fisik. Dalam proses penanganan ikan khususnya ketika ikan dibawa oleh supplier ke tempat produksi, seharusnya posisi ikan ditumpuk dengan urutan ikan-es-ikan-es secara berulang agar daging dan kondisi ikan tetap terjaga. Dalam proses yang tertuang dalam diagram SIPOC, terdapat beberapa proses mengenai penumpukkan ikan yang dapat menyebabkan defect pada ikan salah satunya pada saat ikan dibawa oleh supplier.
Dalam diagram SIPOC, terdapat proses pemberian gas CO pada fillet ikan yang bertujuan untuk mempertahankan warna alami pada ikan segar (Korah et al., 2015). Kurangnya pemahanan mengenai pengisian gas CO pada fillet dan tata letak penempatan fillet saat melakukan pengisian gas CO oleh karyawan dapat mempengaruhi kondisi akhir produk. Berdasarkan wawancara dengan pihak karyawan, pengisian gas CO dilakukan dengan menginjeksi gas ke dalam kemasan plastik roll yang berisi 4-10 fillet ikan. Peletakkan ikan yang bertumpuk dapat menyebabkan tidak meratanya hasil dari pengisian gas CO.
Tabel 2. Hasil penilaian tim terhadap penyebab dominan defect pada fillet ikan kakap putih
Penyebab dominan |
Skor penilaian dari masing-masing anggota tim |
Total Skor |
Peringkat | ||||
Annisa |
Rahmang |
Eko |
Ari |
Kadek | |||
Daging pucat |
2 |
3 |
3 |
2 |
3 |
13 |
3 |
Daging pecah/lembek dan berbau |
4 |
5 |
4 |
3 |
5 |
21 |
1 |
Kulit daging cacat/lecet |
3 |
2 |
2 |
2 |
3 |
12 |
4 |
Pemberian gas CO kurang merata |
3 |
4 |
4 |
4 |
5 |
20 |
2 |
Kemasan vacuum bocor |
3 |
2 |
2 |
1 |
2 |
10 |
5 |
Terdapat serpihan logam pada ikan |
1 |
2 |
2 |
1 |
2 |
8 |
6 |
Supplier Input Process Output Customer
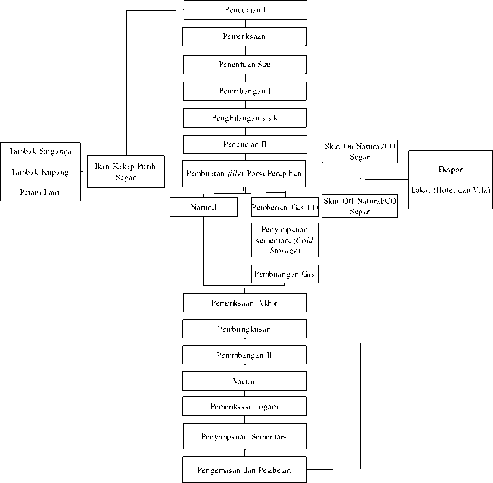
Gambar 1. Diagram SIPOC produksi fillet ikan kakap putih
Keterangan : skor 1 = sangat tidak penting, 2 = tidak penting, 3 = cukup penting, 4 = penting, 5 = sangat penting
ikan kakap putih dapat dilihat pada gambar 2 dan dapat diukur nilai DPMO (Defect per Million Opportunities) sehingga memperoleh nilai sigma yang digunakan sebagai baseline proyek six sigma. Diagram pareto digunakan untuk memprioritaskan produk yang mengalami kecacatan untuk segera dilakukan perbaikan (Magar & Shinde, 2014). Adapun urutan jumlah defect tertinggi sampai terendah yang diperoleh selama penelitian berdasarkan periode waktu minggu ke-empat Desember 2019 sampai dengan Februari 2020 yakni a; daging pecah/lembek dan berbau sebanyak 1.589 unit, b; pemberian gas CO kurang merata sebanyak 726 unit, c; daging pucat sebanyak 83 unit, d; kulit cacat/lecet sebanyak 32 unit, e; kemasan vacuum bocor sebanyak 14 unit, f; terdapat serpihan logam sebanyak 0 unit. Dengan demikian, hasil brainstorming oleh tim manajemen menyepakati dua faktor kritis penyebab utama defect fillet ikan kakap putih yang dikatakan sebagai CTQ (Critical To Quality) potensial, yaitu (1) daging pecah/lembek dan berbau, dan (2) pemberian gas CO yang kurang merata.
Kinerja Existing Sebagai Baseline Proyek Six Sigma
Pengukuran kinerja proses yang sedang berlangsung (existing) atau dalam metode six sigma disebut sebagai tahapan measure. Pada tahapan measure organisasi harus melakukan 2 hal pokok, yaitu (1) memilih dan menentukan karakteristik kualitas kunci yang berhubungan langsung dengan persyaratan pelanggan, dan (2) mengukur kinerja existing (current performance) untuk ditetapkan sebagai baseline pada awal proyek Six Sigma (Soemohadiwidjojo, 2017). Melalui Diagram Pareto dapat diidentifikasi prioritas permasalahan yang harus ditangani, yaitu permasalahan yang paling banyak dan sering terjadi yang mengakibatkan penyimpangan terhadap spesisifikasi yang dipersyaratkan oleh pelanggan (Gunawan & Tannady, 2016). Dengan Diagram Pareto defect fillet
Berdasarkan data yang tertuang pada tabel 3, dapat dilakukan proses perhitungan nilai sigma untuk dijadikan sebagai suatu indikator atau ukuran penentu kinerja proses perusahaan saat ini. Berikut merupakan indikator atau ukuran yang umum digunakan oleh metode six sigma yang terkait dengan defect:
Perhitungan nilai DPMO (Defect per Million Opportunities)
DPMO = JwnLah defectyang ditemukan χ 1 000 000 jumlah unit produk yang dlperlksax jumlah CTQ potensial ' '
= , , x 1.000.000
(25460 x 2)
= 45.463
Perhitungan DPMO sebesar 45.463 yang disebut sebagai indikasi berapa banyak defect akan muncul dalam 1 juta peluang. Nilai DPMO tersebut dikonversikan ke dalam nilai sigma dengan menggunakan tabel konversi six sigma berada pada nilai 3,125-sigma (3σ) dan mempengaruhi total pendapatan akibat biaya terkait produk defect yang
disebut COPQ (Cost of Poor Quality) sebesar 2540% berdasarkan tabel 4 (Prashar, 2014). Maka dapat ditetapkan sebagai baseline proyek six sigma nilai DPMO sebesar 45.463, nilai sigma 3,125 (3σ), nilai COPQ 25-40% biaya pendapatan dan CTQ potensial/faktor kritis penyebab dominan defect yang telah ditetapkan dari ke-enam defect yang ditemukan adalah kondisi daging pecah/lembek dan berbau, pengisian gas CO yang kurang merata merujuk pada data produk defect tertinggi yang ditunjukkan berdasarkan pada gambar 2.
^H Jumlah Defect —•—persentase kumulatif
Gambar 2. Diagram Pareto defect fillet ikan kakap putih
Tabel 3. Produk defect fillet ikan kakap putih yang ditetapkan sebagai baseline proyek six sigma
Periode Minggu ke- |
Kriteria defect (unit) |
Total defect (unit) |
Total Produk si (unit) | |
Daging pecah/lemb ek dan berbau |
Pemberi an gas CO yang kurang merata | |||
IV |
55 |
23 |
78 |
334 |
I |
59 |
70 |
129 |
1198 |
II |
138 |
78 |
216 |
4301 |
III |
233 |
140 |
373 |
4758 |
IV |
563 |
105 |
668 |
5851 |
I |
113 |
59 |
172 |
1837 |
II |
159 |
97 |
256 |
2388 |
III |
103 |
85 |
188 |
1224 |
IV |
166 |
69 |
235 |
3570 |
Total |
1589 |
726 |
2315 |
25460 |
Tabel 4. Hubungan nilai DPMO, nilai sigma dan nilai COPQ
Level Sigma |
DPMO |
Yield |
COPQ |
Kategori |
6 |
3,4 |
99,9997 |
<1% total pendapatan |
World Class |
5 |
230 |
99,977 |
5-15% total pendapatan | |
4 |
6.200 |
99,379 |
15-25% total pendapatan |
Rata-rata industri |
3 |
67.000 |
93,32 |
25-40% total pendapatan | |
2 |
310.000 |
69,2 |
>40% total pendapatan |
Tidak Kompetitif |
Mengidentifikasi Sumber Variasi Mutu Produk Setelah mengetahui kinerja existing perusahaan, diperlukan suatu tahap analisis untuk mengetahui penyebab dari defect pada produk. Menurut Dewi et al (2017) pengukuran kinerja perusahaan memiliki tujuan agar dapat mengetahui sejauh mana perkembangan perusahaan telah tercapai. Agar mencapai kondisi tersebut, pada tahapan Analyze perlu dilakukan pencarian serta analisis terhadap hal-hal yang menjadi akar permasalahan (root-cause) dan dapat menimbulkan variasi pada proses sehingga menyebabkan defect pada produk. Salah satu metode statistik yang banyak digunakan untuk mengidentifikasi variasi adalah fishbone diagram atau diagram sebab akibat. Adapun diagram sebab akibat dalam analisis faktor penyebab defect fillet ikan kakap putih dapat dilihat pada gambar 3.
Fishbone diagram dikelompokkan berdasarkan kategori sebab defect dan masalah yang lebih detail ditempatkan pada cabang dari “tulang ikan” terbesar (Yuniarto et al., 2013). Dari hasil identifikasi pada fishbone diagram yang disepakati berdasarkan hasil brainstorming dan diskusi dalam tim dipilih penyebab utama terjadinya defect pada fillet ikan kakap putih. Ke-enam kategori tersebut dikelompokkan berdasarkan penyebab dari man (petugas/karyawan) yang tidak ada pengalaman, kurangnya training ; machines (alat/mesin) masih manual dan jumlahnya sedikit ; materials (bahan baku) kondisi ikan kakap putih yang kurang baik, dan bahan kemasan yang mudah rusak ; methods (metode) penggunaan SOP dan pemberian informasi yang belum terpadu ; measurements (inspeksi) tidak konsistennya petugas QC (Quality Control) ;
environment (lingkungan) suhu yang tidak sesuai dan kesalahan yang tejadi dianggap lumrah/tanpa ada evaluasi. Dengan demikian dapat diasumsikan bahwa kondisi defect yang terjadi berdasarkan faktor dari keenam kategori tersebut. Fokus perbaikan yang akan dilakukan mengacu pada hasil analisa faktor penyebab dominan defect berdasarkan CTQ potensial.
Gambar 3. Fishbone diagram defect fillet ikan kakap putih
Rekomendasi Perbaikan Untuk Meningkatkan Kinerja Proses
Dalam metode six sigma, setelah melakukan tahapan mengidentifikasi penyebab variasi mutu pada produk maka dapat dikembangkan alternatif solusi dan dipilih solusi yang paling optimum untuk menghasilkan kinerja terbaik. Solusi yang dikembangkan dapat melalui perancangan dan implementasi proses baru. Solusi atau rekomendasi perbaikan disebut improve pada tahapan metode six sigma.
Dalam melakukan perbaikan proses, rekomendasi atau usul yang akan diberikan melalui dua cara yakni menggunakan metode FMEA (Failure Mode and Effect Analysis) dan metode 5W + 1H. Sebelum
merekomendasikan perbaikan yang dilakukan, hal yang harus dilakukan adalah menetapkan target kinerja proses yang diharapkan.
Pada perhitungan kinerja proses yang ditetapkan sebagai baseline six sigma, perusahaan memiliki nilai sigma sebesar 3,125-sigma dengan nilai DPMO 45.463. Agar perusahaan dapat meningkatkan kinerja proses, maka nilai level sigma yang harus dicapai adalah lebih tinggi dari nilai level sigma sebelumnya. Berdasarkan hasil brainstorming dengan tim, target kinerja proses yang diharapkan dapat mencapai level sigma empat (4σ) meskipun perbaikan yang dilakukan secara perlahan dan bertahap. Dengan demikian, pihak perusahaan harus menekan jumlah defect produk hingga mencapai pada level sigma empat (4σ) dengan nilai DPMO sebesar 6.200. Untuk mencapai nilai tersebut, perhitungan dapat dilakukan dengan mensubtitusikan nilai DPMO sebesar 6.400 ke dalam rumus DPMO sebagai berikut :
DPMO =----T2^f^----x ι.ooo.ooo
]umlaħ Output x jumlah CTQ 6.200 = τotal 0efect x ι.ooo.ooo
25460x2
315.704.000 = Total Defect × 1.000.000
Total Defect = 316 unit atau 35 unit per minggu
Total defect sebanyak 316 unit dalam sembilan minggu atau 35 unit per minggu harus dicapai agar mencapai level sigma empat (4σ), sehingga perusahaan diharapkan dapat mengurangi nilai COPQ menjadi 15-25% dari total pendapatan merujuk pada tabel 7.
Failure Mode and Effect Analysis (FMEA) digunakan dengan memberikan nilai kuantitatif terhadap setiap faktor yang diidentifikasi. Pemberian nilai dilakukan melalui sesi diskusi dengan tim penerapan metode six sigma pada setiap penyebab potensial yang diidentifikasi berdasarkan rating severity, rating occurrence dan rating detection yang
kemudian dikalkulasikan mendapat nilai RPN (Risk Priority Number) (Suherman & Cahyana, 2019).
Berdasarkan tabel 5, diperoleh nilai RPN tertinggi sebesar 2730 dengan nilai severity (S) sebesar 14 yang merupakan dampak dari pengaruh kegagalan tersebut, nilai occurrence (O) sebesar 13 yakni seberapa sering kejadian tersebut terjadi, dan nilai detection (D) sebesar 15 yaitu pendeteksian di setiap pengujian. Untuk melakukan rekomendasi perbaikan, dipilih kegagalan potensial yang memiliki nilai RPN tertinggi. Dengan berdiskusi bersama tim, menyepakati tiga jenis penyebab kegagalan potensial dalam dua efek dari kegagalan yang akan direkomendasi untuk perbaikan yakni kurang teliti dalam pemeriksaan dan kesalahan kerja yang menyebabkan daging pecah/lembek dan berbau, serta kemasan bocor yang menyebabkan kurang meratanya pemberian gas CO sehingga daging berwarna pucat.
Tabel 5. Penilaian dengan metode FMEA
Produk yang diharapkan |
Efek dari kegagalan |
Kegagalan Potensial |
Penyebab Kegagalan |
S |
O |
D |
RPN |
Rank |
Daging yang bertekstur padat, kenyal, dan bau amis sewajarnya |
Daging pecah/lembek dan berbau |
Daging pecah dan lembek Kesalahan kerja |
Tertumpuk/terbentur benda lain Kurangnya pengalaman dan pelatihan |
11 14 |
13 13 |
16 15 |
2288 2730 |
4 1 |
Kesalahan dalam pemeriksaan |
SOP ada namun checklist tidak dijalankan |
13 |
11 |
19 |
2717 |
2 | ||
Pembusukkan |
Penurunan suhu akibat kurangnya penanganan |
14 |
13 |
11 |
2002 |
6 | ||
Daging segar dan berwarna |
Daging berwarna pucat |
Perubahan warna |
Gas CO yang kurang merata |
15 |
11 |
13 |
2145 |
5 |
putih |
Kemasan bocor |
Kurangnya informasi terpadu untuk melakukan pengecekan |
16 |
13 |
12 |
2496 |
3 |
-
c. Usulan Perbaikan Dengan Teknik 5W+1H Dalam memberikan rekomendasi perbaikan terlebih dahulu dilakukan diskusi bersama tim dan disertai wawancara dengan pihak-pihak yang terkait.
Adapun tujuannya agar usulan yang diberikan tepat sasaran. Dengan menerapkan teknik 5W+1H sebagai pedoman dalam wawancara mendalam (depthinterview), dapat memecahkan suatu masalah dari berbagai aspek.
Berdasarkan tabel 6, usulan perbaikan yang dapat diberikan pada kondisi kegagalan daging
pecah/lembek dan berbau adalah dengan menjalankan checklist pada SOP yang berlaku dalam rangkaian proses produksi dan memberikan pelatihan dasar seperti penggunaan checklist pada SOP produksi maupun pelatihan-pelatihan lain seperti teknik injeksi gas CO pada produk, teknik pemfilletan bagi karyawan senior dan junior. Dengan menjalankan checklist oleh pihak QC di setiap alur produksi, kondisi defect akan cepat diketahui dan dapat melakukan perbaikan pada rantai produksi ketika ditemukannya defect tersebut. Pelatihan pada karyawan junior hingga senior dapat dilakukan selama rentan waktu enam bulan sekali. Tujuan pelatihan selain memberi pengetahuan dasar mengenai alur produksi, juga dapat melatih skill dari seluruh karyawan yang bertugas agar menjadi lebih terampil dan lebih produktif (Rudhaliawan, 2013). Pada tabel 7, usulan perbaikan yang dapat dilakukan adalah mengecek setiap kemasan yang digunakan dalam mengemas produk. Adapun dengan tujuan agar tidak terjadi kontaminasi produk terhadap udara luar, mempermudah proses pemvakuman, dan menjaga gas CO agar mempertahankan warna segar pada ikan (Hanidah et al., 2018). Hal ini dilakukan pada setiap alur proses pengemasan, bahkan pengecekkan dilakukan ketika produk diberi gas CO. Hal utama yang dilakukan agar usulan ini dapat dijalankan dengan baik yakni memberikan informasi terpadu mengenai bagaimana pengecekkan yang semestinya dilakukan.
Tabel 6. Usulan perbaikan pada kondisi daging pecah/lembek dan berbau
Jenis |
5W+1H |
Deskripsi/Tindakan |
Checklist dijalankan oleh operator | ||
Tujuan Utama |
What (apa) |
Diadakan pelatihan dasar cara penggunaan checklist dan proses injeksi pada produk bagi seluruh karyawan senior maupun junior |
Alasan Kegunaan |
Why (mengapa) |
Adanya keakuratan data pada saat pemeriksaan |
Seluruh karyawan terampil di setiap tugas pada saat produksi | ||
Where (dimana) |
Di area produksi | |
Lokasi |
Di PT I Am Be U Mina Utama | |
Waktu |
When |
Ketika rangkaian proses produksi berlangsung |
(kapan) |
Setiap 6 bulan sekali | |
Who (siapa) |
Staff Quality Control (QC) | |
Orang |
Seluruh karyawan senior maupun junior | |
How (bagaiman a) |
Menempatkan satu orang staff QC di setiap rangkaian proses | |
Metode |
Mengundang pembicara ahli baik dari daerah maupun pusat atau memberi kesempatan pelatihan junior oleh senior |
Tabel 7. Usulan perbaikan pada kondisi gas CO kurang merata
Jenis |
5W+1H |
Deskripsi/Tindakan |
Tujuan Utama |
What (apa) |
Pengecekkan disetiap kemasan produk |
Alasan Kegunaan |
Why (mengapa) |
Agar gas CO merata dan dapat mencegah udara dari luar masuk dan merusak produk |
Lokasi |
Where (dimana) |
Line proses filleting, pengisian gas CO dan proses pengemasan |
Waktu |
When (kapan) |
Disetiap proses pengemasan produk, baik sebelum pengisian gas CO dan proses pengemasan akhir |
Orang |
Who (siapa) |
Petugas QC, pengemasan dan pengisian gas CO |
Metode |
How (bagaimana) |
Memberikan informasi panduan mengenai kondisi kemasan yang mudah bocor, memeriksa disetiap proses pengemasan |
KESIMPULAN DAN SARAN
Kesimpulan
Faktor penyebab utama defect pada proses produksi fillet ikan kakap putih adalah daging pecah/lembek dan berbau serta pemberian gas CO yang kurang merata sehingga mempengaruhi warna daging yang ditetapkan berdasarkan pengamatan serta analisis bersama tim. Penyebab utama dominan defect ditemukan berdasarkan kondisi defect tertinggi dari enam kategori defect.
Dengan menggunakan tabel FMEA dan Teknik 5W+1H, diperoleh usulan perbaikan yakni menjalankan checklist sesuai prosedur di setiap alur produksi, memberi pelatihan dasar tata cara menjalankan checklist pada SOP, pelatihan berupa proses injeksi CO pada produk, pelatihan pada proses pemfilletan kepada karyawan senior dan junior, serta mengecek kemasan produk secara berkala agar tidak adanya kemasan yang bocor.
Saran
Dalam melakukan penelitian ini diperlukan catatan defect yang lebih akurat sehingga memudahkan dalam menganalisa produk serta proses control dalam melakukan perbaikan. Tahap control pada tahapan DMAIC di Metode Six Sigma dilakukan agar mengetahui pengaruh metode six sigma terhadap proses perbaikan yang dilakukan. Tahap ini
adalah menjalankan usulan perbaikan yang telah direkomendasikan.
DAFTAR PUSTAKA
Caesaron, D., & Simatupang, S. Y. P. (2015). Implementasi pendekatan DMAIC untuk perbaikan proses produksi pipa PVC (studi kasus PT. Rusli Vinilon). Jurnal Metris, 16(2), 91-96.
Dewi, D. A. P. M. C., Widia, I. W., & Aviantara, I. G. N. A. Pengaruh Sistem Manajemen Keamanan Pangan ISO 22000: 2005 Terhadap Kinerja Perusahaan. Jurnal BETA (Biosistem dan Teknik Pertanian), 5(1), 93-102.
Emilasari, D., & Vanany, I. (2007). Aplikasi six sigma pada produk clear file di perusahaan stationary. Jurnal Teknik Industri, 9(1), 27-36.
Farmayanti, N., & Dinarwan, D. (2006). Perspektif Six Sigma dalam Analisis Manajemen Kualitas Kasus Produksi Fish Fillet di PT Dharma Samudra Fishing Industry, Jakarta. Buletin Ekonomi Perikanan, 6(3), 11025.
Gunawan, C. V., & Tannady, H. (2016). Analisis Kinerja Proses dan Identifikasi Cacat Dominan Pada Pembuatan Bag Dengan Metode Statistical Proses Control (Studi Kasus : Pabrik Alat Kesehatan PT.XYZ, Serang, Banten).
J@Ti Undip: Jurnal Teknik Industri, 11 (1), 914.
Hanidah, I. I., Setasih, I. S., Santoso, M. B., & Mardawati, E. (2018). Upaya Peningkatan Nilai Jual “Pindang Cue” Melalui Teknik Pengemasan. Dharmakarya, 7(1), 14-18.
Korah, H., Ijong, F. G., & Suwetja, I. K. (2015). Salmonella occurrence and myoglobin (mb) in frozen smoked tuna. AQUATIC SCIENCE & MANAGEMENT, 3(2), 45-49.
Latief, Y., & Utami, R. P. (2010). Penerapan Pendekatan Metode Six Sigma Dalam Penjagaan Kualitas Pada Proyek Konstruksi. MAKARA of Technology Series, 13(2), 67– 72.
Magar, V. M., & Shinde, V. B. (2014). Application of 7 Quality Control ( 7 QC ) Tools for Continuous Improvement of Manufacturing Processes. International Journal of Engineering Research and General Science, 2(4), 364–371.
Nurjanah, A. A., Sudirman, S., & Tarman, K. (2014).
Pengetahuan Bahan Baku Hasil Perairan.
Pangaribuan, B. M., & Handayani, N. U. (2016). Analisis Penyebab Cacat Produksi Roma Kelapa Pada Mesin Oven Dengan Metode Failure Modes Effects Analysis ( Fmea ). Engineering Journal, 1–9.
Prashar, A. (2014). Adoption of Six Sigma DMAIC to reduce cost of poor quality. International Journal of Productivity and Performance Management, 63(1), 103–126.
Rudhaliawan, V. M. (2013). Pengaruh Pelatihan terhadap Kemampuan Kerja dan Kinerja Karyawan (Studi pada Karyawan PT. Telkom Indonesia, Tbk Kandatel Malang). Jurnal Administrasi Bisnis, 4(2).
Rohmatulloh, R., Kusumastuti, R., & Shiddiq, J. A. (2017). Penentuan Kriteria Evaluasi Kinerja Widyaiswara Menggunakan Nominal Group Technique. Jurnal Teknik Industri, 17(2), 51.
Sedana, I., Widia, I., & Yulianti, N. (2015).
Pengaruh Teknik Bleeding Dan Jenis Media Pendingin Terhadap Mutu Fillet Ikan Kakap Putih(Lates Calcarifer Bloch). BETA (Biosistem Dan Teknik Pertanian), 3(2), 1–11.
Soemohadiwidjojo, A. T. (2017). Six Sigma Metode Pengukuran Kinerja Perusahaan Berbasis Statistik. Jakarta: Raih Asa Sukses.
Suherman, A., & Cahyana, B. J. (2019).
Pengendalian Kualitas Dengan Metode Failure Mode Effect And Analysis ( FMEA ) Dan Pendekatan Kaizen untuk Mengurangi Jumlah Kecacatan dan Penyebabnya. Seminar Nasional Sain Dan Teknologi, 1–9.
Try, N., Sutanaya, A., Ketut, P., Kencana, D., & Arda, G. (2018). Aplikasi asap cair tempurung kelapa mampu meningkatkan umur simpan fillet ikan tuna. Jurnal Beta (Biosistem Dan Teknik Pertanian), 6(2), 82–89.
Wahyani, W., Chobir, A., & Rahmanto, D. D.
(2010). Penerapan Metode Six Sigma Dengan Konsep Dmaic Sebagai Alat Pengendali Kualitas. Prosiding Seminar Nasional Manajemen Teknologi XII, 1–14.
Widiyawati, S., & Assyahlafi, S. (2017). Perbaikan produktivitas perusahaan rokok melalui pengendalian kualitas produk dengan metode six sigma. Journal of Industrial Engineering Management, 2(2), 32-38.
Yuniarto, H. A., Akbari, A. D., & Masruroh, N. A.
(2013). Perbaikan Pada Fishbone Diagram Sebagai Root Cause Analysis Tool. Jurnal Teknik Industri, 3(3), 217–224.
Zulkarnain, M., Purwanti, P., & Indrayani, E.
(2013). Analysis of Aquaculture Production Value Effect To Gross Domestic Product of Fisheries Sector in. Jurnal ECSOFiM, 1(1), 52–68.
44
Discussion and feedback