Aplikasi Waste Assessment Model (WAM) Pada Proses Perencanaan Anggaran Menggunakan Sistem SILUNA
on
Majalah Ilmiah Teknologi Elektro, Vol.22, No.1, Jan-Juni 2023
DOI: https://doi.org/10.24843/ MITE.2023.v22i01.P04 29
Aplikasi Waste Assessment Model (WAM) Pada Proses
Perencanaan Anggaran Menggunakan Sistem SILUNA
Ni Wayan Lusiani1, Made Sudarma2, Lie Jasa3
[Submission: 10-12-2023, Accepted:22-01-2023]
Abstract— One strategy to improve the quality of both procedures and products is to implement an audit process. One of the audit techniques that can be applied is waste detection. Waste is a habit that by itself has no added value. The auditing method used to uncover waste is called lean. The main goal of lean is to find and eliminate operations that provide no value to the process. The Waste Assessment Model (WAM) is a tool that Lean uses to identify waste. The use of WAM is focused on planning to identify waste in the budget process utilizing the SILUNA system in the Planning Section of the Planning and Finance Bureau of Udayana University. The wastes with the highest scores were defects, which accounted for the first order waste with a percentage of 19.79%, and inventories, which accounted for the second order waste with a percentage of 16.35%.
Key Wordi— Lean; Waste; Waste Assessment Model
Intisari— Peningkatan suatu kualitas baik produk maupun proses dapat dilakukan dengan menerapkan proses audit. Salah satu proses audit yang dapat dilakukan adalah dengan mengidentifikasi adanya suatu pemborosan. Pemborosan itu sendiri merupakan suatu proses yang tidak bernilai tambah. Metode audit yang digunakan untuk mengidentifikasi terdapatnya pemborosan adalah Lean. Penentuan dan eliminasi suatu proses yang tidak memberikan suatu nilai tambah merupakan fokus utama dari Lean. Dalam penerapannya, Lean memiliki metode untuk mengidentifikasi suatu pemborosan, metode tersebut adalah Waste Assessment Model (WAM). Penerapan WAM difokuskan untuk mengidentifikasi pemborosan dalam proses perencanaan anggaran menggunakan sistem SILUNA pada Bagian Perencanaan di Biro Perencanaan dan Keuangan Universitas Udayana. Penelitian ini mendapatkan hasil berupa 2 (dua) pemborosan dengan nilai paling tinggi, yaitu : defect merupakan waste urutan pertama dengan persentase 19,79% dan waste yang berada pada urutan berikutnya adalah inventory dengan persentase 16,35%.
Kata Kunci— Lean; Waste; Waste Assessment Model
Kegiatan dalam perencanaan anggaran dilakukan oleh organisasi yang mampu menghasilkan suatu rencana kerja dan
anggaran (RKA). Anggaran dalam organisasi sendiri merupakan suatu kondisi yang menggambarkan pendapatan, aktivitas dan belanja suatu program. Perencanaan anggaran sendiri harus disusun secara sistematis dan harus meliputi seluruh kegiatan dalam organisasi. Perencanaan anggaran tersebut akan berlaku dalam jangka waktu satu tahun mendatang. Penyusunan suatu rencana kerja dan anggaran pada pemerintah mengacu pada Peraturan Pemerintah Nomor 20 Tahun 2004 mengenai Rencana Kerja Pemerintah, serta Peraturan Pemerintah Nomor 21 Tahun 2004 tentang RKA-KL.
Universitas Udayana sebagai salah satu Universitas negeri yang ada di Bali, juga diharuskan untuk melaksanakan penyusunan anggaran seperti yang telah ditetapkan oleh pemerintah pusat. Salah satu Biro yang ada diantara 4 biro di Universitas Udayana adalah BPKU yang merupakan kepanjangan dari Biro Perencanaan dan Keuangan. BPKU terdiri dari 2 bagian, yaitu Perencanaan dan Keuangan. Pelaksanaan tugas dalam hal urusan perencanaan merupakan tugas utama dari bagian Perencanaan [1]. Untuk mendukung pelaksanaan kegiatan tersebut, bagian perencanaan memanfaatkan beberapa system informasi, diantaranya SILUNA (Sistem Informasi Solusi Perencanaan), UKT Ku pada menu TRPNBP yang digunakan untuk mengetahui target rencana penerimaan pada tahun berikutnya dan SILAKIN (Sistem Informasi Laporan Kinerja).
Teknologi informasi yang dipergunakan dalam membantu pelaksanaan kegiatan dalam pelaksanaan segala urusan perencanaan perlu dilakukan audit, salah satu diantaranya dalam bidang tata kelola. Tata Kelola TI memiliki pengertian proses pelaksanaan untuk meninjau dan mengendalikan keputusan kemampuan TI dalam memastikan adanya suatu nilai yang diberikan dari pemangku kepentingan dalam organisasi [2].
Audit dapat diterapkan melalui berbagai metode, misalkan dengan audit yang bertujuan untuk meningkatkan produk dan proses dapat dilakukan dengan cara mengidentifikasi terjadinya pemborosan atau waste. Pemborosan atau waste didefinisikan sebagai aktivitas bisnis apa pun yang menghasilkan sumber daya tetapi tidak menambah nilai seperti yang didefinisikan oleh pelanggan [3]. Metode yang diterapkan untuk dapat mengidentifikasi waste ialah Lean.
Lean yaitu teknik manajemen yang diakui di bidang manufaktur, prinsip-prinsip dasarnya juga dapat disesuaikan dan diterapkan pada proses layanan. Lean juga mulai dikembangkan melalui Lean IT sebagai disiplin khusus untuk meningkatkan nilai pelanggan dan mengurangi biaya produk dan layanan teknologi informasi. Salah satu konsep yang digunakan dalam mengeleminasi pemborosan adalah Lean.
p-ISSN:1693 – 2951; e-ISSN: 2503-2372
Penelitian ini menerapkan metode Waste Assessment Model (WAM). Hubungan antara 7 pemborosan untuk dapat mengidentifikasi peringkat pemborosan didapatkan melalui kuesioner[4].
Beberapa penelitan telah menerapkan Lean dengan metode WAM untuk melakukan identifikasi mengenai apa saja pemborosan yang ditemukan dalam suatu proses baik dalam bidang jasa ataupun bidang manufaktur. Beberapa penelitian tersebut antara lain : Penelitian yang dilakukan oleh [5] menerapkan metode WAM untuk mengidentifkasi adanya pemborosan kemudian dianalisis untuk mengetahui akar penyebab pemborosan dengan menggunakan fishbone diagram. Penelitian ini menghasilkan peringkat pemborosan dengan urutan peringkat dari tinggi ke rendah adalah : defect (22,70%), overproduction (18,32%), inventory (17,56), motion (14,12%), transportation (13,10%), waiting (9,68) dan process (4,52).
Penelitian kedua yang dijadikan acuan adalah penelitian yang dilakukan [6]. Penelitian ini bertujuan untuk mengidentifikasi adanya pemborosan pada produksi sehingga dapat memberikan usulan perbaikan berdasarkan pemborosan yang ditemukan. Nilai persentase akhir yang didapatkan dari masing-masing ke-tujuh pemborosan yaitu : defect (27%), overproduction (18%), inventory (14%), motion (13%), transportation (11%), process (8%), dan waiting (8%).
Penelitian berikutnya adalah penelitian yang dilakukan oleh [7] dalam bidang jasa pelayanan. Penelitian dilakukan pada PT. Dakota Buana Semesta yang bergerak pada bidang pelayanan. Tujuan penelitian adalah untuk mengidentifikasi pemborosan dan mencarikan solusi dari masalah yang ditemukan. Penerapan Lean Six Sigma dilakukan dengan current state mapping. Pemetaan seluruh informasi yang ada di perusahaan menggunakan process activity mapping untuk mengetahui aktivitas yang memiliki nilai tambah dan yang tidak memiliki nilai tambah. Pemborosan yang ditemukan yaitu waiting for the next step. Akar penyebab dari pemborosan yang ditemukan dianalisis menggunakan 5 why sehingga dapat memberikan solusi perbaikan.
Lean dengan metode WAM juga dilakukan oleh [8] untuk meminimalkan pemborosan. Pendekatan Lean menggunakan metode value stream mapping (VSM), Waste Relationship Matrix (WRM) dan Waste Assesment Questionnaire (WAQ). Analisis pemborosan dilakukan menggunakan fishbone dan 5W+1H. Peringkat pemborosan yang dihasilkan yaitu defect 16,49%, transportation 16,36%, dan process 14,82%. Analisis akar penyebab dilakukan dengan fishbone dan 5W+1H, sehingga dapat memberikan perbaikan untuk meminimalisasi pemborosan yang ditemukan.
Berdasarkan penelitian-penelitian sebelumnya, penelitian ini dilakukan untuk mendapatkan tujuan yang hampir sama yaitu dengan mengidentifikasi adanya pemborosan pada proses perencanaan anggaran yang dilakukan menggunakan SILUNA dengan menggunakan pendekatan Lean untuk melakukan pemeringkatan pemborosan menggunakan metode Waste Assessment Model (WAM). Penelitian sebelumnya yang dijadikan acuan menerapkan WAM pada bidang manufaktur, sedangkan penelitian ini diterapkan pada bidang jasa. Peneliti mengharapkan dengan dilakukannya identifikasi pemborosan pada proses perencanaan anggaran mampu meningkatkan kinerja dengan melakukan perbaikan pada pemborosan yang bersifat dominan.
-
A. Audit Sistem Informasi
Audit sistem informasi merupakan suatu rangkaian prosedur sistematis untuk mencapai dan menilai suatu bukti yang rasional atas aset SI dalam menetapkan tingkat kesesuaian antara SI dan kriteria yang diinginkan [9][10].
Penelitian lain [11] mengatakan bahwa audit merupakan kegiatan yang dilakukan untuk mengevaluasi dan mengukur kesesuaian kinerja dari suatu proses terhadap prosedur yang telah ada atau yang telah diuji.
Suksesnya suatu tata kelola dalam perusahaan bergantung terhadap tata kelola TI yang telah dilakukan [12]. Penerapan TI yang selaras dengan tujuan dan strategi organisai dapat diraih dengan melakukan pengelolaan TI yang baik pula [12].
-
B. Lean
Langkah pertama dalam pemecahan masalah adalah mendeteksi masalah itu sendiri. Proses Lean adalah menemukan masalah dalam proses yang akan terwujud dalam bentuk pemborosan [3].
Cara sederhana untuk mendeteksi pemborosan adalah dengan menggunakan diagram alir, mengamati proses, mengumpulkan data yang relevan, dan menganalisa langkah-langkah proses. Lean dimulai sebagai sarana untuk meningkatkan produksi dalam bidang manufaktur, tetapi kemudian ditemukan bahwa penerapan Lean sama efektifnya ketika diterapkan pada industri jasa [3].
Lean lebih berpusat untuk melakukan identifikasi dan menghilangkan aktivitas dengan tidak memiliki nilai tambah (non value added activites) untuk mendapatkan keuntungan dan integritas pada bidang produksi (manufaktur), desain, operasi atau jasa serta manajemen rantai pasok yang memiliki keterkaitan secara langsung dengan konsumen [13] [14][15].
Lean Enterprise yaitu suatu konsep lean dimana diaplikasikan dalam semua lini organisasi. Sedangkan Lean Manufacturing yaitu konsep lean dimana diaplikasikan dalam bidang industri, dan lean service sendiri yaitu konsep lean dimana diaplikasikan pada aspek jasa [14]. Metode pendekatan untuk mengidentifikasi pemborosan yang dipergunakan adalah Waste Assessment Model (WAM).
WAM merupakan sebuah model yang dikembangkan untuk menyederhanakan pencarian dari sebuah permasalahan pemborosan serta melakukan identifikasi untuk mengelemeninasi pemborosan [5].
-
C. Identifikasi Pemborosan (Waste)
-
1. Pemborosan (Waste)
Pemborosan, berarti muda dalam Bahasa Jepang, yaitu semua perbuatan yang tidak melahirkan nilai [16].
Terdapat tujuh pemborosan yang kerap kali ditemukan pada bidang jasa, dan disandingkan dengan pemborosan yang ditemukan pada bidang manufaktur [14] :
Penjelasan tentang 7 pemborosan pada bidang jasa [14]:
-
a. Produksi yang berlebihan
Pengerjaan tugas melebihi yang dibutuhkan, dengan kata lain pengerjaan suatu tugas dilakukan sebelum adanya permintaan dari konsumen.
tabel I
Tipe Pemborosan Pada Perusahaan Jasa dan Manufaktur
Tipe Pemborosan |
Lambang |
Produksi yang berlebihan |
O |
Inventori |
I |
Cacat |
D |
Gerakan |
M |
Transportasi |
T |
Proses yang berlebihan |
P |
Menunggu |
W |
-
b. Inventori
Tidak adanya suatu penyeragaman atau standarisasi pada suatu proses pengerjaan tugas, termasuk tidak adanya pembakuan yang digunakan dalam waktu penyelesaian tugas.
-
c. Cacat
Interaksi yang tidak mampu dibangun dengan baik kepada konsumen, terdapat kesalahpahaman, kurangnya memahami pelanggan, tidak menghiraukan pelanggan, tidak ramah atau kurang ramah, tidak sopan atau kurang sopan dan kurangnya pemahaman mengenai layanan ataupun produk yang dipasarkan.
-
d. Gerakan
Adanya suatu tindakan yang tidak dibutuhkan dalam memberikan pelayanan kepada konsumen seperti adanya metode/pendekatan yang diterapkan dalam penyelesaian tugas.
-
e. Transportasi
Adanya suatu tindakan berupa Gerakan yang tidak diperlukan dari sumber daya yang dapat berupa orang ataupun barang dan adanya gerakan fisik, misalkan diharuskan untuk bergerak ke tempat yang berbeda.
-
f. Proses yang berlebihan
Terdapat adanya suatu kegiatan atau proses yang diterapkan kepada konsumen yang tidak memiliki suatu nilai tambah. Misalkan terdapat pengisian data yang serupa secara berulang, mendapatkan informasi yang serupa serta mengisi atau menanggapi terlalu banyak kuesioner/pertanyaan yang berulang kali menyebabkan konsumen beralih karena dianggap membuang waktu.
-
g. Menunggu
Dapat berwujud adanya waktu tunggu yang harus dirasakan atau dialami oleh konsumen, baik dalam hal adanya proses antrian yang lama untuk mendapatkan suatu layanan, informasi, pengiriman ataupun proses yang tidak sinkron berdasarkan waktu yang sudah ditetapkan. Pemborosan dalam hal adanya waktu tunggu dapat merugikan perusahaan karena mampu memberikan dampak berupa hilangnya kepercayaan konsumen.
-
2. Penerapan Lean dengan Metode Waste Assessment Model (WAM)
Penerapan WAM diterapkan untuk melakukan identifikasi pemborosan dengan melakukan pembobotan sesuai dengan
Wayan Lusiani: Aplikasi Waste Assessment Model…
31 pemborosan yang terjadi. Penerapan metode WAM
diaplikasikan untuk memudahkan dalam proses identifikasi waste [14][17]. WAM lebih banyak dipergunakan dalam konsep penerapan lean manufacture. Perusahaan jasa tidak terlepas dari pemborosan, tujuh pemborosan dalam bidang jasa dan manufaktur tidak terlalu berbeda. WAM terdiri dari Hubungan antara 7 pemborosan (SWR), Matrik Hubungan Antar Pemborosan (WRM) dan Waste Assessment Questionnaire (WAQ) [14] [17].
Data didapatkan dengan melakukan penyebaran kuesioner pembobotan. Penyebaran kuesioner dilakukan untuk mendapatkan keterkaitan antar pemborosan dan mendapatkan bobot dari masing-masing pemborosan.
Penelitian dilaksanakan di Universitas Udayana, pada Bagian Perencanaan di Biro Perencanaan dan Keuangan. Proses yang diobservasi adalah proses perencanaan anggaran menggunakan sistem SILUNA. Skematik dari penelitian yang dilakukan ditunjukkan melalui Gambar1.
Gambar 1. Skematik Penelitian.
Penjelasan mengenai skematik penelitian berdasarkan Gambar 1, sebagai berikut :
-
A. Studi Pustaka.
Penelitian dimulai dengan melakukan studi pustaka untuk mengetahui dan memahami langkah-langkah dalam melakukan analisis pemborosan. Mencari referensi dan penyusunan pertanyaan kuesioner yang akan dilakukan untuk mendapatkan data yang diperlukan juga dilakukan pada tahapan ini. Referensi dan studi Pustaka yang dilakukan berfokus kepada
p-ISSN:1693 – 2951; e-ISSN: 2503-2372
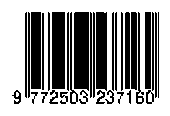
.
Pendekatan Lean dengan metode WAM (Waste Assessent Model).
Kuesioner yang telah disusun kemudian dibagikan dengan teknik sampling purposive dengan kriteria operator SILUNA dan pemangku kepentingan pada Bagian Perencanaan. Pertanyaan kuesioner terdiri dari 2 jenis yaitu kuesioner untuk mengetahui hubungan antar 7 pemborosan (kuesioner SWR) dan kuesioner pemborosan (WAQ).
Adapun tahapan dalam pelaksanaan penelitian dengan pendekatan Lean menggunakan metode WAM, yaitu :
-
1. Menentukan Hubungan antar Pemborosan
Hubungan antar pemborosan didapatkan dengan menyebarkan kuesioner SWR yang telah disusun sebelumya. Total terdapat 25 pertanyaan untuk menunjukkan masing-masing hubungan antar pemborosan. Hasil kuesioner akan dikonversi ke dalam nilai yang telah ditentukan sesuai dengan studi Pustaka dan referensi yang telah ditemukan untuk menghasilkan Waste Relationship Matrix.
tabel II
Pertanyaan Kuesioner Untuk Hubungan 7 Pemborosan (SWR)
No |
Pertanyaan |
Pilihan Jawaban |
1 |
Apakah overproduction menghasilkan inventory? |
a. Selalu |
b. Kadang-kadang | ||
c. Jarang |
Tabel II menunjukkan contoh pertanyaan yang digunakan untuk mengetahui hubungan antar 7 pemborosan. Pertanyaan yang diajukan dibagi menjadi 6 jenis pertanyaan dengan hubungan yang berbeda untuk masing-masing pemborosan. Pertanyaan kuesioner yang disusun berdasarkan pada penelitian yang telah dilakukan sebelumnya oleh [18].
-
2. Pembuatan Matrix Hubungan Antar Pemborosan.
Hasil dari penyebaran kuesioner SWR dikoneversi ke dalam nilai untuk menghasilkan matrik hubungan antar pemborosan. Hasil kuesioner yang didapatkan kemudian di total dan dikonversi ke dalam nilai keterkaitan antar pemborosan. Jenis hubungan berdasarkan skor total dari nilai tertinggi 20 dengan jenis hubungan Absolutely Necessary/sangat-sangat perlu, hingga nilai terendah 0 dengan jenis hubungan No Relation/tidak berhubungan.
tabel III
Pertanyaan Kuesioner Pemborosan (WAQ)
N o |
Aspek dan Daftar Pertanyaan |
Jawaban |
Jenis Pertanyaan | ||
Ya (Y)/ Sedang (S)/ Tidak (T) | |||||
Man | |||||
1 |
Apakah pihak manajemen sering melakukan rolling atau pemindahan pekerja untuk semua pekerjaan sehingga satu jenis pekerjaan bisa dilakukan oleh semua pekerja? |
Y |
S |
T |
To Motion |
-
3. Pemeringkatan Pemborosan dengan Waste Assessment
Questioner (WAQ)
Kuesioner WAQ disusun untuk menghasilkan peringkat dari pemborosan. Pertanyaan yang dipergunakan disesuaikan
dengan kondisi di lapangan, jadi tidak semua pertanyaan yang didapatkan pada saat melakukan studi pustaka dipergunakan pada penelitian ini.
Tabel III menunjukkan contoh pertanyaan kuesioner yang dilakukan untuk mendapatkan peringkat pemborosan dari aspek yang diteliti. Todal terdapat 25 pertanyaan untuk mengetahui jenis pemborosan yang terjadi.
-
B. Penerapan Lean dengan Metode WAM.
Langkah-langkah dalam melakukan identifikasi pemborosan menggunakan pendekatan Lean dengan metode WAM dilakukan dengan tahapan :
-
1. Pengumpulan Data dan Pembuatan Kuesioner
Pembuatan kuesioner SWR disusun pertama kali untuk mendapatkan hasil dari keterkaitan atau hubungan untuk masing-masing pemborosan. Kuesioner disusun berdasarkan acuan dari tahapan studi pustaka yang telah dilakukan sebelumnya
Berdasarkan penyebaran kuesioner yang telah dilakukan, pengumpulan data awal didapatkan untuk selanjutnya diolah, dianalisis dan dihasilkan kesimpulan dari penelitian ini.
-
• Kuesioner Seven Waste Relationship (SWR).
Masing-masing pertanyaan pada kuesioner memiliki bobot jawaban, bobot tersebut ditotal dan ditentukan tingkat keterkaitannya berdasarkan konversi rentang skor keterkaitan antar 7 pemborosan [4][14][19][5].
TABEL IV
Konversi Nilai Keterkaitan Antar Pemborosan
Rentang |
Penjelasan Hubungan |
Lambang |
17 s.d 20 |
“Sangat - sangat perlu” |
A |
13 s.d 16 |
“Sangat penting” |
E |
09 s.d 12 |
“Penting” |
I |
05 s.d 08 |
“Biasa saja” |
O |
01 s.d 04 |
“Tidak penting” |
U |
0 |
“Tidak berhubungan” |
X |
Tabel IV menunjukkan rentang skor, jenis hubungan dan simbol untuk melakukan konversi dari total nilai yang telah didapatkan. Jenis hubungan berdasarkan skor total dari nilai tertinggi 20 dengan jenis hubungan Absolutely Necessary/sangat-sangat perlu, hingga nilai terendah 0 dengan jenis hubungan No Relation/tidak berhubungan.
-
• Kuesioner Pemborosan (WAQ).
Pengumpulan data awal dari kuesioner WAQ dilakukan dengan menggunakan tabel seperti terlihat pada tabel V.
TABEL V
Format Nilai Awal Berdasarkan WAQ
No |
Kate -gori |
Hubungan |
O |
I |
D |
M |
T |
P |
W |
1 |
Man |
T. Motion | |||||||
2 |
F. Motion |
Tabel V menunjukkan data awal yang didapatkan berdasarkan penyebaran kuesioner. Jawaban yang didapatkan dikonversi kedalam angka sesuai dengan jawaban yang dberikan dengan ketentuan “Ya” bernilai 1, pilihan “Sedang” bernilai 0.5, serta pilihan “tidak” yang memiliki nilai 0 [4].
-
2. Pengolahan Data
Setelah melakukan pengumpulan data melalui kuesioner, selanjutnya akan dilakukan pengolahan data sesuai dengan metode Lean yang digunakan yaitu metode WAM. Langkah-langkah dalam pengolahan data yang telah didapatkan berdasarkan kuesioner menggunakan pendekatan Lean dengan metode WAM, dilakukan dengan tahapan :
-
• Seven Waste Relationship (SWR)
Perhitungan mengenai keterkaitan antar tujuh pemborosan (Seven Waste Relationship) diterapkan dengan membagikan kuesioner. Hasil dari kuesioner akan diidentifikasi untuk mengetahui hubungan antar waste berdasarkan rentang nilai pada Tabel IV.
Hasil keterkaitan antar waste yang dihasilkan dalam penelitian ini terlihat pada Tabel VI.
TABEL VI
Hasil Keterkaitan Antar Pemborosan
Pertanyaan |
Nilai |
Hubungan Keterkaitan |
O - I |
1 |
U |
O - D |
1 |
U |
O - M |
1 |
U |
O - T |
1 |
U |
O - W |
1 |
U |
I - O |
6 |
O |
I - D |
6 |
O |
I - M |
4 |
U |
I - T |
6 |
O |
D - O |
4 |
U |
D - I |
4 |
U |
D - M |
6 |
O |
D - T |
4 |
U |
D - W |
6 |
O |
M - I |
4 |
U |
M - D |
4 |
U |
M - W |
4 |
U |
M - P |
4 |
U |
T - O |
4 |
U |
T - I |
4 |
U |
T - D |
4 |
U |
T - M |
8 |
O |
Wayan Lusiani: Aplikasi Waste Assessment Model…
33
T - W |
6 |
O |
P - O |
6 |
O |
P - I |
4 |
U |
P - D |
6 |
O |
P - M |
4 |
U |
P - W |
4 |
U |
W - O |
4 |
U |
W - I |
4 |
U |
W - D |
4 |
U |
Berdasarkan Tabel VI bahwa dari hasil penelitian dengan memberikan kuesioner berupa pertanyaan mengenai keterkaitan antar waste didapatkan bahwa total skor yang dihasilkan berada pada rentang antara 1 hingga 6, sehingga tingkat keterkaitan yang didapatkan terdiri dari unimportant dan ordinary closeness.
-
• Waste Relationship Matrix (WRM)
Tahapan selanjutnya adalah WRM, dengan mengubah hasil dari keterkaitan antar tujuh pemborosan dan menjadikan nilai huruf yang dihasilkan kedalam sebuah matrik keterkaitan.
Berdasarkan pada Tabel VI maka disusunlah WRM berdasarkan hubungan antar pemborosan. WRM pada proses perencanaan anggaran dapat dilihat pada Tabel VII.
TABEL VII
Matrik Keterkaitan antar pemborosan
F/T |
O |
I |
D |
M |
T |
P |
W |
O |
A |
U |
U |
U |
U |
X |
U |
I |
O |
A |
O |
U |
O |
X |
X |
D |
U |
U |
A |
O |
U |
X |
O |
M |
X |
U |
U |
A |
X |
U |
U |
T |
U |
U |
U |
O |
A |
X |
O |
P |
O |
U |
O |
U |
X |
A |
U |
W |
U |
U |
U |
X |
X |
X |
A |
WRM memperlihatkan jenis pemborosan satu mampu memberikan imbas pada pemborosan yang lain. Masing-masing baris memperlihatkan imbas atau pengaruh satu pemborosan tertentu terhadap ke-6 pemborosan lainnya. Sedangkan masing-masing kolom memperlihatkan pemborosan yang terpengaruh oleh pemborosan lainnya.
Setelah dihasilkan matrik seperti Tabel VII, dilanjutkan dengan mengkonversi WRM kedalam nilai, dimana A=10, E=8, I=6, O=4, U=2 dan X=0 [4][14][20]. Hasil konversi WRM kedalam angka dapat dilihat pada Tabel VIII.
p-ISSN:1693 – 2951; e-ISSN: 2503-2372
TABEL VIII
Waste Matrix Value
F/T |
O |
I |
D |
M |
T |
P |
W |
Total |
% |
O |
10 |
2 |
2 |
2 |
2 |
0 |
2 |
20 |
13,33 |
I |
4 |
10 |
4 |
2 |
4 |
0 |
0 |
24 |
16,00 |
D |
2 |
2 |
10 |
4 |
2 |
0 |
4 |
24 |
16,00 |
M |
0 |
2 |
2 |
10 |
0 |
2 |
2 |
18 |
12,00 |
T |
2 |
2 |
2 |
4 |
10 |
0 |
4 |
24 |
16,00 |
P |
4 |
2 |
4 |
2 |
0 |
10 |
2 |
24 |
16,00 |
W |
2 |
2 |
2 |
0 |
0 |
0 |
10 |
16 |
10,67 |
Total |
24 |
22 |
26 |
24 |
18 |
12 |
24 |
150 |
100 |
% |
16, 00 |
14, 67 |
17, 33 |
16, 00 |
12, 00 |
8, 00 |
16, 00 |
100 |
Pada Tabel VIII di atas terlihat bahwa nilai from inventory, from defect, from transportation dan from process mendapatkan hasil persentase maksimum, yakni sebanyak 16,00%. Hal ini dapat dikatakan bahwa waste tersebut pada saat terjadi, memiliki imbas yang lumayan besar sehingga dapat menimbulkan dan menyebabkan waste yang lain. Sedangkan nilai to defect, to overproduction, to waiting dan to motion menghasilkan nilai persentase maksimal, yakni berturut-turut 17,33%, 16,00%, 16,00% dan 16,00%. Hal ini dapat dikatakan bahwa waste defect, overproduction, motion dan waiting adalah jenis pemborosan dimana paling banyak disebabkan oleh jenis pemborosan yang lain.
-
• Waste Assessment Questionnaire (WAQ)
Langkah pengukuran peringkat pemborosan dengan WAQ, yaitu [21][22]:
-
a. Melakukan perhitungan jumlah pertanyaan yang digunakan dan mengelompokkan berdasarkan “from” dan “to”. Huruf “F” pada jenis pertanyaan melambangkan “from”dan huruf “T” melambangkan “to”.
TABEL IX
Jumlah dan Pertanyaan WAQ
Pertanyaan |
Total (Ni) |
F. Motion |
7 |
F. Waiting |
2 |
F. Defect |
6 |
F. Overproduction |
1 |
F. Process |
2 |
T. Waiting |
3 |
T. Defect |
1 |
T. Motion |
3 |
Total |
25 |
Tabel IX memperlihatkan jumlah pertanyaan yang digunakan pada penelitian ini, dengan jumlah 25 pertanyaan. Masing-masing pertanyaan mewakili from dan to, dengan rincian : from motion berjumlah 7 pertanyaan, from waiting
berjumlah 2 pertanyaan, from defect berjumlah 6 pertanyaan, from overproduction berjumlah 1 pertanyaan, from process berjumlah 2 pertanyaan, to waiting berjumlah 3 pertanyaan, to defect berjumlah 1 pertanyaan, dan to motion berjumlah 3 pertanyaan.
Kategori pertanyaan dalam WAQ terbagi menjadi empat, yaitu : method, man, machine, dan material. Jawaban dari masing-masing pertanyaan terdiri dari 3, yaitu : pilihan “Ya” bernilai 1, pilihan “Sedang” bernilai 0.5, serta pilihan “tidak” yang memiliki nilai 0 [4].
-
b. Memberikan nilai awal dari masing-masing pertanyaan berdasarkan waste matrix value (Tabel VIII).
TABEL X
Nilai Awal Berdasarkan WAQ
Kategori |
Hubungan |
O |
I |
D |
M |
T |
P |
W |
Man |
T. Motion |
2 |
2 |
4 |
10 |
4 |
2 |
0 |
F. Motion |
0 |
2 |
2 |
10 |
0 |
2 |
2 | |
F. Defect |
2 |
2 |
10 |
4 |
2 |
0 |
4 | |
F. Motion |
0 |
2 |
2 |
10 |
0 |
2 |
2 | |
F. Motion |
0 |
2 |
2 |
10 |
0 |
2 |
2 | |
F. Defect |
4 |
2 |
10 |
4 |
2 |
0 |
4 | |
Material |
F.Defect |
4 |
2 |
10 |
4 |
2 |
0 |
4 |
T. Waiting |
4 |
0 |
4 |
2 |
4 |
2 |
10 | |
F. Defect |
4 |
2 |
10 |
4 |
2 |
0 |
4 | |
Machine |
F. Waiting |
2 |
2 |
2 |
0 |
0 |
0 |
10 |
F. Waiting |
2 |
2 |
2 |
0 |
0 |
0 |
10 | |
T.Motion |
2 |
2 |
4 |
10 |
4 |
2 |
0 | |
Method |
T. Waiting |
4 |
0 |
4 |
2 |
4 |
2 |
10 |
T. Defect |
4 |
4 |
10 |
2 |
2 |
4 |
2 | |
F.Motion |
0 |
2 |
2 |
10 |
0 |
2 |
2 | |
F.Defect |
4 |
2 |
10 |
4 |
2 |
0 |
4 | |
F.Motion |
0 |
2 |
2 |
10 |
0 |
2 |
2 | |
T.Waiting |
4 |
0 |
4 |
2 |
4 |
2 |
10 | |
F. Process |
4 |
2 |
4 |
2 |
0 |
10 |
2 | |
T. Motion |
4 |
2 |
4 |
10 |
4 |
2 |
0 | |
F. Motion |
0 |
2 |
2 |
10 |
0 |
2 |
2 | |
F. Motion |
0 |
2 |
2 |
10 |
0 |
2 |
2 | |
F. Overproduction |
10 |
4 |
4 |
4 |
4 |
0 |
4 | |
F. Process |
4 |
2 |
4 |
2 |
0 |
10 |
2 | |
F. Defect |
4 |
2 |
10 |
4 |
2 |
0 |
4 | |
Total Skor |
68 |
48 |
124 |
140 |
42 |
50 |
98 |
-
c. Membagi masing-masing nilai awal yang telah dihasilkan dengan total jumlah dari jenis pertanyaan (Ni), hal ini dilakukan untuk menghapuskan dampak variasi dari jumlah total pertanyaan yang ada dari setiap jenis pertanyaan.
Majalah Ilmiah Teknologi Elektro, Vol.22, No.1, Jan-Juni 2023 DOI: https://doi.org/10.24843/ MITE.2023.v22i01.P04
TABEL XI
Jumlah Pertanyaan (Ni) dan Total Skor (Sj) Serta Frekuensi (Fj)
Kategori |
Hubungan |
Ni |
O |
I |
D |
M |
T |
P |
W |
Man |
T.Motion |
3 |
0, 67 |
0, 67 |
1, 33 |
3, 33 |
1, 33 |
0, 67 |
0, 00 |
F. Motion |
7 |
0, 00 |
0, 29 |
0, 29 |
1, 43 |
0, 00 |
0, 29 |
0, 29 | |
F. Defect |
6 |
0, 33 |
0, 33 |
1, 67 |
0, 67 |
0, 33 |
0, 00 |
0, 67 | |
F. Motion |
7 |
0, 00 |
0, 29 |
0, 29 |
1, 43 |
0, 00 |
0, 29 |
0, 29 | |
F. Motion |
7 |
0, 00 |
0, 29 |
0, 29 |
1, 43 |
0, 00 |
0, 29 |
0, 29 | |
F. Defect |
6 |
0, 67 |
0, 33 |
1, 67 |
0, 67 |
0, 33 |
0, 00 |
0, 67 | |
Material |
F. Defect |
6 |
0, 67 |
0, 33 |
1, 67 |
0, 67 |
0, 33 |
0, 00 |
0, 67 |
T. Waiting |
3 |
1, 33 |
0, 00 |
1, 33 |
0, 67 |
1, 33 |
0, 67 |
3, 33 | |
F. Defect |
6 |
0, 67 |
0, 33 |
1, 67 |
0, 67 |
0, 33 |
0, 00 |
0, 67 | |
Machine |
F. Waiting |
2 |
1, 00 |
1, 00 |
1, 00 |
0, 00 |
0, 00 |
0, 00 |
5, 00 |
F. Waiting |
2 |
1, 00 |
1, 00 |
1, 00 |
0, 00 |
0, 00 |
0, 00 |
5, 00 | |
T. Motion |
3 |
0, 67 |
0, 67 |
1, 33 |
3, 33 |
1, 33 |
0, 67 |
0, 00 | |
Method |
T. Waiting |
3 |
1, 33 |
0, 00 |
1, 33 |
0, 67 |
1, 33 |
0, 67 |
3, 33 |
T. Defect |
6 |
0, 67 |
0, 67 |
1, 67 |
0, 33 |
0, 33 |
0, 67 |
0, 33 | |
F. Motion |
7 |
0, 00 |
0, 29 |
0, 29 |
1, 43 |
0, 00 |
0, 29 |
0, 29 | |
F. Defect |
6 |
0, 67 |
0, 33 |
1, 67 |
0, 67 |
0, 33 |
0, 00 |
0, 67 | |
F. Motion |
7 |
0, 00 |
0, 29 |
0, 29 |
1, 43 |
0, 00 |
0, 29 |
0, 29 | |
T. Waiting |
3 |
1, 33 |
0, 00 |
1, 33 |
0, 67 |
1, 33 |
0, 67 |
3, 33 | |
F. Process |
2 |
2, 00 |
1, 00 |
2, 00 |
1, 00 |
0, 00 |
5, 00 |
1, 00 | |
T. Motion |
3 |
1, 33 |
0, 67 |
1, 33 |
3, 33 |
1, 33 |
0, 67 |
0, 00 | |
F. Motion |
7 |
0, 00 |
0, 29 |
0, 29 |
1, 43 |
0, 00 |
0, 29 |
0, 29 | |
F. Motion |
7 |
0, 00 |
0, 29 |
0, 29 |
1, 43 |
0, 00 |
0, 29 |
0, 29 | |
F. Over-production |
1 |
10, 00 |
4, 00 |
4, 00 |
4, 00 |
4, 00 |
0, 00 |
4, 00 | |
F. Process |
2 |
2, 00 |
1, 00 |
2, 00 |
1, 00 |
0, 00 |
5, 00 |
1, 00 | |
F. Defect |
1 |
4, 00 |
2, 00 |
10, 00 |
4, 00 |
2, 00 |
0, 00 |
4, 00 | |
Total Skor (Sj) |
30, 33 |
16, 33 |
40, 00 |
35, 67 |
16, 00 |
16, 67 |
35, 67 | ||
Frekuensi (Fj) |
18 |
22 |
25 |
23 |
14 |
16 |
22 |
Tabel XI menghasilkan nilai skor total (Sj) dan nilai frekuensi (Fj) untuk masing-masing pemborosan setelah membagi nilai awal dari masing-masing pertanyaan dengan jumlah pertanyaan (Ni).
-
d. Nilai yang diperoleh dari kuesioner sebesar (0, 0.5 atau 1) dimasukkan, kemudian dicari rata-rata berdasarkan jumlah responden. Rata-rata nilai tersebut akan menjadi
Wayan Lusiani: Aplikasi Waste Assessment Model…
35 bobot untuk mendapatkan perhitungan skor terbaru, melakukan perhitungan total skor (sj) dan menghitung frekuensi (fj) yang baru. Hasil yang didapatkan dapat dilihat pada Tabel XII.
TABEL XII
Hasil Perhitungan Total Skor (sj) dan Frekuensi (fj)
Kategori |
Hubungan |
Weight |
O |
I |
D |
M |
T |
P |
W |
Man |
T. Motion |
0, 38 |
0, 25 |
0, 25 |
0, 50 |
1, 25 |
0, 50 |
0, 25 |
0, 00 |
F. Motion |
0, 75 |
0, 00 |
0, 21 |
0, 21 |
1, 07 |
0, 00 |
0, 21 |
0, 21 | |
F. Defect |
0, 75 |
0, 25 |
0, 25 |
1, 25 |
0, 50 |
0, 25 |
0, 00 |
0, 50 | |
F. Motion |
0, 75 |
0, 00 |
0, 21 |
0, 21 |
1, 07 |
0, 00 |
0, 21 |
0, 21 | |
F. Motion |
0, 50 |
0, 00 |
0, 14 |
0, 14 |
0, 71 |
0, 00 |
0, 14 |
0, 14 | |
F. Defect |
1, 00 |
0, 67 |
0, 33 |
1, 67 |
0, 67 |
0, 33 |
0, 00 |
0, 67 | |
Material |
F. Defect |
0, 50 |
0, 33 |
0, 17 |
0, 83 |
0, 33 |
0, 17 |
0, 00 |
0, 33 |
T. Waiting |
0, 75 |
1, 00 |
0, 00 |
1, 00 |
0, 50 |
1, 00 |
0, 50 |
2, 50 | |
F. Defect |
1, 00 |
0, 67 |
0, 33 |
1, 67 |
0, 67 |
0, 33 |
0, 00 |
0, 67 | |
Machine |
F. Waiting |
0, 13 |
0, 13 |
0, 13 |
0, 13 |
0, 00 |
0, 00 |
0, 00 |
0, 63 |
F. Waiting |
1, 00 |
1, 00 |
1, 00 |
1, 00 |
0, 00 |
0, 00 |
0, 00 |
5, 00 | |
T. Motion |
0, 00 |
0, 00 |
0, 00 |
0, 00 |
0, 00 |
0, 00 |
0, 00 |
0, 00 | |
Method |
T. Waiting |
1, 00 |
1, 33 |
0, 00 |
1, 33 |
0, 67 |
1, 33 |
0, 67 |
3, 33 |
T. Defect |
1, 00 |
0, 67 |
0, 67 |
1, 67 |
0, 33 |
0, 33 |
0, 67 |
0, 33 | |
F. Motion |
1, 00 |
0, 00 |
0, 29 |
0, 29 |
1, 43 |
0, 00 |
0, 29 |
0, 29 | |
F. Defect |
0, 63 |
0, 42 |
0, 14 |
0, 23 |
0, 15 |
0, 05 |
0, 00 |
0, 00 | |
F. Motion |
0, 50 |
0, 00 |
0, 14 |
0, 14 |
0, 71 |
0, 00 |
0, 14 |
0, 14 | |
T. Waiting |
0, 75 |
1, 00 |
0, 00 |
1, 00 |
0, 50 |
1, 00 |
0, 50 |
2, 50 | |
F. Process |
0, 88 |
1,75 |
0, 88 |
1, 75 |
0, 88 |
0, 00 |
4, 38 |
0, 88 | |
T. Motion |
0, 63 |
0, 83 |
0, 42 |
0, 83 |
2, 08 |
0, 83 |
0, 42 |
0, 00 | |
F. Motion |
0, 50 |
0, 00 |
0, 14 |
0, 14 |
0, 71 |
0, 00 |
0, 14 |
0, 14 | |
F. Motion |
0, 75 |
0, 00 |
0, 21 |
0, 21 |
1, 07 |
0, 00 |
0, 21 |
0, 21 | |
F. Over-production |
0, 63 |
6, 25 |
2, 50 |
2, 50 |
2, 50 |
2, 50 |
0, 00 |
2, 50 | |
F. Process |
0, 50 |
1, 00 |
0, 50 |
1, 00 |
0, 50 |
0, 00 |
2, 50 |
0, 50 | |
F. Defect |
0, 50 |
2, 00 |
1, 00 |
5, 00 |
2, 00 |
1, 00 |
0, 00 |
2, 00 | |
Total (sj) |
19, 54 |
9, 91 |
24, 71 |
20, 32 |
9, 63 |
11, 23 |
23, 69 | ||
Frekuensi (fj) |
17 |
21 |
24 |
22 |
13 |
15 |
21 |
Tabel XII memperlihatkan nilai total skor (sj) dan frekuensi p-ISSN:1693 – 2951; e-ISSN: 2503-2372
(fj) yang telah dikalikan dengan bobot yang didapatkan melalui rata-rata jawaban kuesioner responden.
-
e. Perhitungan nilai awal untuk masing-masing pemborosan (Yj) dengan mengalikan total skor dengan frekuensi. Menghitung Pj Factor dengan mengalikan total “from” dan “to”pada WRM. Memprosentasikan nilai final result sehingga didapatkan peringkat untuk masing-masing pemborosan. Persamaan yang digunakan untuk mendapatkan hasil akhir adalah [4]:
Yjfinai= Yj X pj = (jjxfyx (%Fromj x %Toj) (1)
-
C. Hasil dan Pembahasan
Analisis dilakukan setelah mendapatkan hasil pengolahan data dengan metode WAM. Hasil yang akan dihasilkan nanti berupa pemeringkatan dari 7 pemborosan yang ditemukan berdasarkan penyebaran kuesioner. Hasil analisis akan ditampilkan dalam bentuk tabel dan grafik sesuai dengan nilai persentase dari masing-masing pemborosan.
-
D. Kesimpulan
Setelah semua tahapan dilaksanakan, hasil akhir dari penelitian ini akan diambil kesimpulan. Kesimpulan ini nantinya diharapkan mampu menjadi acuan untuk melakukan perbaikan pada proses perencanaan anggaran menggunakan SILUNA.
Metode WAM digunakan untuk mendapatkan hasil berupa peringkat pemborosan, dengan menggunakan kuesioner Seven Waste Relationship untuk mendapatkan hubungan dari 7 pemborosan dan kuesioner tipe pemborosan yang dibagikan kepada responden. [4].
Berdasarkan langkah-langkah penerapan yang telah dijelaskan sebelumnya, hasil yang didapatkan berupa peringkat pemborosan yang disajikan dalam Tabel XII.
TABEL XIII
Hasil Final WAM
O |
I |
D |
M |
T |
P |
W | |
Nilai (Yj) |
0,61 |
0,58 |
0,59 |
0,54 |
0,56 |
0,63 |
0,63 |
Pj Factor |
213, 33 |
234, 67 |
277, 33 |
192, 00 |
192, 00 |
128, 00 |
170, 67 |
Final Result (Yj Final) |
129, 80 |
135, 95 |
164, 49 |
104, 60 |
107, 36 |
80, 87 |
108, 21 |
Final Result (%) |
15, 61% |
16, 35% |
19, 79% |
12, 58% |
12, 91% |
9, 73% |
13, 02% |
Ranking |
3 |
2 |
1 |
6 |
5 |
7 |
4 |
Hasil yang didapatkan berdasarkan Tabel XIII berupa nilai dengan menggunakan persamaan (1). Kemudian hasil Yj Final dirubah menjadi persentase kemudian dilakukan perangkingan berdasarkan nilai persentase tersebut.
Berdasarkan Tabel XIII dapat dilihat bahwa peringkat pemborosan yang didapatkan dari peringkat pertama sampai
peringkat ke tujuh berturut-turut adalah : jenis pemborosan defect dengan nilai 19,79%, inventory dengan nilai 16,35%, overproduction dengan nilai 15,61%, waiting dengan nilai 13,02%, transportation dengan nilai 12,91%, motion dengan nilai 12,58%, dan waste processing dengan nilai 9,73%.
Peringkat pemborosan dalam bentuk grafik akan disajikan sebagai berikut :
Peringkat Waste
25,00
20,00
15,00
10,00
5,00 0,00

Waste
Gambar 2. Grafik Peringkat Hasil Perhitungan Waste Assessment
Sama seperti Tabel XIII, gambar 2 menunjukkan hasil peringkat dari 7 waste yang telah dilakukan perhitungan sebelumnya. Berdasarkan perhitungan yang telah dilakukan penelitian ini berfokus pada 2 (dua) tipe pemborosan kritis yang dihasilkan, yaitu berturut-turut: defect dan inventory.
Pengolahan awal penelitian ini yang ditujukan untuk mengidentifikasi adanya pemborosan, didapatkan hasil bahwa terdapat 2 tipe pemborosan yang memiliki nilai tertinggi, berturut-turut adalah: defect merupakan pemborosan peringkat pertama dengan persentase 19,79%, pemborosan urutan kedua adalah inventory dengan persentase 16,35%. Nilai tersebut menunjukkan bahwa tipe pemborosan defect dan inventory merupakan tipe pemborosan yang paling dominan, berdasarkan nilai perhitungan WAM. Tipe pemborosan defect dan inventory merupakan tipe pemborosan yang paling sering ditemukan pada proses perencanaan anggaran menggunakan SILUNA. Dengan mengetahui bahwa tipe pemborosan defect dan inventory merupakan pemborosan yang paling dominan dan sering terjadi, diharapkan dapat membantu dalam menemukan solusi yang tepat sehingga mampu meningkatkan kinerja pada proses perencanaan.
Referensi
-
[1] Kementerian Kesehatan RI, “Berita Negara,” Peratur. Menteri
Kesehat. Republik Indones. Nomor 4 Tahun 2018, vol. 151, no. 2, pp. 10–17, 2018.
-
[2] K. Sofa, T. Lathif, M. Suryanto, R. R. Suryono, and J. Timur,
“Audit Tata Kelola Teknologi Informasi Menggunakan Kerangka Kerja Cobit 5 Pada Dinas Pekerjaan Umum Kabupaten Tanggamus,” J. Teknol. dan Sist. Inf., vol. 1, no. 1, pp. 39–46, 2020, [Online]. Available: http://jim.teknokrat.ac.id/index.php/sisteminformasi
-
[3] A. S. Akhilesh N Singh, Lean IT Principles To Practice Toyota
Way To Create Value for The Customer & Wealth for IT Organization. NCR Delhi, INdia: Notion Press 2018, 2018.
Majalah Ilmiah Teknologi Elektro, Vol.22, No.1, Jan-Juni 2023 DOI: https://doi.org/10.24843/ MITE.2023.v22i01.P04 [4] E. Altayany, “ANALISIS PRIORITAS PERBAIKAN GUNA
MEMINIMASI WASTE DOMINAN PADA PROSES PRODUKSI DENGAN FAILURE MODE EFFECT ANALYSIS ANALYTICAL HIERARCHY PROCESS (FMEA AHP) (STUDI KASUS: PT LEZAX NESIA JAYA),” 2018.
-
[5] A. Naziihah, J. Arifin, and B. Nugraha, “Identifikasi Waste
Menggunakan Waste Assessment Model (WAM) di Warehouse Raw Material PT. XYZ,” J. Media Tek. dan Sist. Ind., vol. 6, no. 1, p. 30, 2022, doi: 10.35194/jmtsi.v6i1.1599.
-
[6] A. R. Putri, L. Herlina, and P. F. Ferdinant, “Identifikasi Waste
Menggunakan Waste Assessment Model ( WAM ) Pada Lini Produksi PT . KHI Pipe Industries,” J. Untirta, vol. 5, no. 1, pp. 3– 7, 2017, [Online]. Available: http://www.jurnal.untirta.ac.id/index.php/jiss/article/view/1537
-
[7] R. M. S. Alfajri and Y. Muchtiar, “Penerapan Lean Six Sigma Di
Jasa Pelayanan Pengiriman Barang Pt. Dakota Buana Semesta,” J. Fac. Ind. Technol. Bung Hatta Univ., vol. 18, 2021.
-
[8] A. R. Irwan Setiawan, “Penerapan Lean Manufacturing Untuk
Meminimalkan Waste Dengan Menggunakan Metode VSM Dan WAM Pada PT XYZ,” Semin. Nas. Penelit. LPPM UMJ, pp. 1–10, 2021.
-
[9] I. B. A. E. M. Putra, R. S. Hartati, and Y. Divayana, “Audit Sistem
Informasi E-Kinerja Dinas Kependudukan Dan Pencatatan Sipil Kota Denpasar,” Maj. Ilm. Teknol. Elektro, vol. 19, no. 1, p. 107, 2020, doi: 10.24843/mite.2020.v19i01.p16.
-
[10] R. Patawala and A. D. Manuputty, “Audit Sistem Informasi pada
Dinas Perpustakaan dan Kearsipan Kota Salatiga,” Sebatik, vol. 25, pp. 42–49, 2021.
-
[11] C. D. Oktaviana Soleman, M. Sudarma, and N. Pramaita,
“Literature Review Penerapan Teknologi Informasi dan Metode Pengukuran Pada Audit Kepuasan Pelanggan,” Maj. Ilm. Teknol. Elektro, vol. 20, no. 2, p. 289, 2021, doi: 10.24843/mite.2021.v20i02.p13.
-
[12] R. Wijaya, H. Honni, and H. Pratama, “Audit Sistem Informasi
Pada Pt Walepay Finansial Teknologi Menggunakan Kerangka Kerja Cobit 4.1 Dan Balanced Scorecard,” JBASE - J. Bus. Audit Inf. Syst., vol. 3, no. 1, pp. 14–21, 2020, doi:
37
10.30813/jbase.v3i1.2058.
-
[13] H. Budiwati, “Pendekatan Lean Six Sigma Dalam Penentuan
Prioritas Perbaikan Layanan Bank Berdasarkan Persepsi, Harapan Dan Kepentingan Nasabah,” J. Manaj., vol. 21, no. 1, p. 1, 2017, doi: 10.24912/jm.v21i1.144.
-
[14] A. Nur Kholis, “Implementasi Lean Service Di Industri
Telekomunikasi Guna Meningkatkan Produktivitas (Studi Kasus: PT. Telkom Witel Yogyakarta),” pp. 1–9, 2020.
-
[15] L. Sihotang, “Peningkatan Service Quality Menggunakan Lean Six
Sigma Studi Kasus PT PLN (Persero) Unit Layanan Pelanggan (ULP) Perbaungan,” Tesis, pp. 1–104, 2019.
-
[16] M. Shodiq and A. Khannan, “Analisis Penerapan Lean
Manufacturing untuk Menghilangkan Pemborosan di Lini Produksi PT Adi Satria Abadi Pendahuluan,” J. Rekayasa Sist. Ind., vol. 4, no. 1, pp. 47–54, 2015.
-
[17] T. Satria, “Perancangan Lean Manufacturing dengan Menggunakan
Waste Assessment Model (WAM) dan VALSAT untuk Meminimumkan Waste (Studi Kasus: PT. XYZ),” J. Rekayasa Sist. Ind., vol. 7, no. 1, p. 55, 2018, doi: 10.26593/jrsi.v7i1.2828.55-63.
-
[18] A. Nur Kholis, “Implementasi Lean Service di Industri
Telekomunikasi Guna Meningkatkan Produktivitas (Studi KAsus : PT. Telkom Witel Yogyakarta),” pp. 1–9, 2020.
-
[19] R. C. Guntoro, T. P. Adhiana, D. T. Industri, F. Teknik, and U.
Jenderal, “Identifikasi Waste Menggunakan Metode Waste Assessment Model,” Pros. Semin. Nas. dan Call Pap., vol. 4, no. November, pp. 41–48, 2019.
-
[20] R. Alfiansyah, Waste Identification With Waste Assessment Model
for Implementing Lean Manufacturing To Improve Production Process (Case Study on Glove Production Process). 2018.
-
[21] Riza Nur Madaniyah, “MINIMASI WASTE DAN LEAD TIME
PADA PROSES PRODUKSI LEAF SPRING DENGAN PENDEKATAN LEAN MANUFACTURING,” 2017.
-
[22] S. Irwan and A. Rahman, “Penerapan Lean Manufacturing Untuk
Meminimalkan Waste Dengan Menggunakan Metode VSM Dan WAM Pada PT XYZ,” Semin. Nas. Penelit. LPPM UMJ, pp. 1–10, 2021.
Wayan Lusiani: Aplikasi Waste Assessment Model…
p-ISSN:1693 – 2951; e-ISSN: 2503-2372
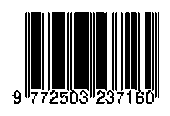
[ HALAMAN INI SENGAJA DIKOSONGKAN]
ISSN 1693 – 2951
Wayan Lusiani: Aplikasi Waste Assessment Model…
Discussion and feedback