The Effect of Firing Temperature on Water Absorption and Flexural Strength on The Preparation of Stoneware Ceramic (Coded-BL1P)
on
Buletin Fisika Vol 20 No. 1 February 2019 : 25 – 28
Pengaruh Suhu Bakar terhadap Penyerapan Air dan Kuat Lentur pada Pembuatan Keramik Stoneware (Kode-BL1P)
The Effect of Firing Temperature on Water Absorption and Flexural Strength on The Preparation of Stoneware Ceramic (Coded-BL1P)
-
1 Program Studi Fisika, Fakultas MIPA, Universitas Udayana, Kampus Bukit Jimbaran, Badung, Bali, Indonesia 80361
-
2 Unit Pelaksana Teknis Laboratorium Badan Pengkajian dan Penerapan Teknologi (BPPT) – Balai Teknologi Industri Kreatif Keramik (BTIKK), Suwung Kauh, Tanah Kilap, Denpasar selatan, Bali Indonesia
Email: aguspermanaputrasujana@gmail.com; *suardanaputu@unud.ac.id; totok.nugroho@bppt.go.id
Abstrak – Telah diteliti pengaruh suhu pembakaran terhadap penyerapan air dan kuat lentur dalam pembuatan keramik stoneware kode BL1P. Keramik dibuat dalam bentuk balok uji dengan bahan dari Borneo Clay Noodle, RRC Feldspar, Kaolin Belitung, Belitung Quartz, Ballclay Bantur, Bentonite, dan Talk dengan metode casting sederhana. Balok uji dibakar pada empat variasi suhu, yaitu 850, 900, 1000, dan 1200 oC. Dari hasil pengukuran penyerapan airnya, ditemukan bahwa peningkatan suhu bakar dari 850 oC menjadi 1200 oC mengakibatkan penurunan penyerapan air dari 18,3% sampai dengan 5,5%, sedangkan pengukuran kuat lenturnya menunjukkan peningkatan dari 11,6 kg/cm2 hingga 19,8 kg/cm2.
Kata kunci: keramik stoneware, suhu bakar, daya serap air, kuat lentur.
Abstract – It has been investigated the effect of firing temperature on water absorption and flexural strength in the manufacture of BL1P code stoneware ceramics. Ceramics are made in the form the test block bar with materials from of Borneo Clay Noodle, PRC Feldspar, Kaolin Belitung, Belitung Quartz, Ballclay Bantur, Bentonite, and Talk with a simple casting method. The block bar of the molds was burned at four temperature variations, i.e. 850, 900, 1000, and 1200 oC. From the results of measurements of its water absorption, it was found that the increase in firing temperature from 850 oC to 1200 oC showed a decrease in water absorption from 18.3% to 5.5%, while the measurement of its flexural strength showed an increase in flexural strength of 11.6 kg/cm2 to 19.8 kg/cm2.
Key words: stoneware ceramics, firing temperature, water absorption, flexural strength.
body) yang sangat plastis dengan susut kering tidak lebih dari 5%, tidak ada kecenderungan retak dan pecah selama pengeringan, tidak mengandung alkali yang menimbulkan busa serta bahan organik dalam jumlah besar [3]. Sifat pasca bakar pada suhu 1222 oC sampai dengan 1305 oC (pada cone 6 sampai cone 10) susut bakar tidak lebih dari 6%, penyerapan air 1% - 5%, warna coklat sampai oranye muda dengan permukaan yang halus[4].
Masa bodi stoneware dibuat dengan mencampurkan beberapa bahan mentah sesuai dengan kebutuhan [5], yaitu: a) Bahan pengisi, berupa mineral kuarsa (SiO2). Kuarsa merupakan salah satu mineral silika, yaitu chalcedon, dymite, cristobalite, opal, lechatelierite, coesite dan stishovite [6]. Kuarsa memiliki titik leleh 1715 oC, tahan asam dan basa serta keras. Bahan ini berpengaruh terhadap kekuatan massa bodi keramik, baik sebelum maupun setelah pembakaran. b) Bahan pengikat, berupa mineral-mineral lempung (clay) dari kaolinit (Al2O3.2SiO2.2H2O). titik leleh bahan ini 1740 oC. Ballclay, talk dan bentonite juga termasuk bahan pengikat [7]. c) Bahan pelebur, yaitu bahan-bahan yang mengandung logam alkali atau alkali tanah seperti feldspar kapur, dolomit. Feldspar yang paling banyak digunakan berupa feldspar kalium-barium yang mempunyai struktur kristal monoklinik dan kelompok feldspar natrium-kalsium yang mempunyai struktur kristal triklinik [8]. Titik lebur feldspar 1250 oC [2]. Adanya logam alkali atau alkali tanah dalam feldspar membantu silika dan alumina melebur dan meleleh pada suhu yang lebih rendah. Leburan feldspar membentuk cairan gelas yang mengisi pori-pori, mengikat partikel yang lebih besar. Leburan feldspar memegang peranan sebagai pasta yang menyatukan partikel menjadi padat setelah proses pendinginan.
Telah dibuat komposisi bodi keramik stoneware dengan kode BL1 dari campuran nodle clay Kalimantan, kaolin, ball clay, bentonite, feldspar RRT, talk dan kuarsa Belitung dengan suhu pembakaran 1250 oC [9]. Diperoleh bahwa rata-rata nilai penyerapan air (PA) sebesar (3,69 ± 0,15)% . Pada penelitian ini telah dilakukan pengukuran daya serap air dan kekerasan dari keramik stoneware massa bodi BL1P untuk variasi suhu pembakaaran 850 – 1200 oC.
Dalam penelitian ini digunakan formula massa bodi keramik seperti pada Tabel 1, jumlah total massa bodi keramik adalah 2000 gram. Bahan-bahan yang digunakan dalam penelitian ini ditunjukkan pada Tabel 1. Semua bahan dicampur kemudian ditambahkan air sebanyak 330 mL sehingga terbentuk adonan keramik basah yang homogen. Setelah adonan keramik didiamkan selama 24 jam kemudian dicetak menjadi bentuk balok-balok dengan metode kasting sederhana, hasilnya kita sebut sebagai balok-balok uji. Balok-balok uji didiamkan di dalam ruangan terbuka sampai diperoleh kondisi kering, yaitu ukuran balok-balok uji relatif tidak berubah.
Tabel 1. Formula persentase bahan keramik kode BL1P.
No |
Bahan |
Persentase |
1 |
Noodle Clay Kalimantan |
40,0% |
2 |
Feldspar RRC |
13,5% |
3 |
Kaolin Belitung |
13,5% |
4 |
Kuarsa Belitung |
20,0% |
5 |
Ballclay Bantur |
10,0% |
6 |
Bentonite |
1,0% |
7 |
Talk |
2,0% |
Balok-balok uji selanjutnya dibakar pada 4 variasi suhu, yaitu pada 850, 900, 1000 dan 1200 oC selama 24 jam. Massa bodi keramik dalam kondisi kering ditimbang dan dicatat sebagai berat masa bodi kering k (gram). Selajutnya balok-balok uji kering ini direndam di dalam air hingga tidak ada gelembung udara yang ke luar dari balok-balok uji. Untuk tujuan ini balok-balok uji direndam selama 24 jam. Tahap berikutnya balok-balok uji basah ditimbang dan dicatat sebagai berat masa bodi keramik basah w (gram). Dari dua hasil pengukuran tersebut selanjutnya dihitung daya serap air PA (%) dengan persamaan (1) [9, 10] w - k
Peresapan air (PA) = x 100% (1)
k
Kuat lentur masa bodi keramik ini ditentukan dengan metode tekan tiga titik (three points bending). Untuk tujuan ini maka dilakukan pengukuran tebal t (cm), lebar l (cm) dan panjang antar penyangga keramik p (cm), serta berat beban (load) N (kg) pada saat terjadi kegagalan struktur (structural failure), yaitu pada saat keramik patah. Kekuatan lentur σ dihitung dengan persamaan (2) [11, 12].
(2)
dengan σ dalam kg/cm2.
Dari hasil pengukuran berat massa bodi keramik stoneware BL1P dalam keadaan kering k dan dalam keadaan basah w telah dilakukan perhitungan daya serapnya terhadap air dengan hasil perhitungan dengan persamaan (1) ditunjukkan pada kolom kedua pada Tabel 2. Dengan data hasil pengukuran tebal t, lebar l dan panjang antar penyangga keramik p serta berat beban N pada saat keramik patah hasil perhitungan besar kuat lentur keramik stoneware BL1P dengan persamaan (2) ditunjukkan pada kolom ketiga dalam Tabel 2.
Tabel 2. Kemampuan serap terhadap air dan Kekuatan lentur keramik stoneware BL1P.
Suhu bakar keramik, T (oC) Daya serap air, PA (%) Kuat lentur, σ (kg/cm2)
850 |
18,3 ± 0,3 |
11,6 ± 0,8 |
900 |
14,3 ± 0,2 |
12,4 ± 1,2 |
1000 |
13,1 ± 0,4 |
13,6 ± 0,1 |
1200 |
5,5 ± 0,1 |
19,8 ± 2,8 |
Berdasarkan data pada Tabel 2 selanjutnya dibuat grafik antara suhu bakar keramik stoneware BL1P dan daya serapnya serta grafik antara suhu bakar keramik stoneware BL1P dan kuat lenturnya, yang masing-masing ditunjukkan pada Gambar 1 dan Gambar 2.
20
18
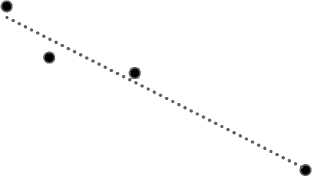
16
14
12
10
8
6
4
2
0 I I I I I I I I I I I I I I I I I I I I I I I I I I I I I I I I I I I I I I I I I I I I I I
800 850 900 950 1000 1050 1100 1150 1200 1250
Suhu, T (oC)
Gambar 1. Grafik suhu bakar dan daya serap air keramik stoneware BLIP. Garis putus-putus adalah hasil fitting regresi linier.
Pada Gambar 1 tampak bahwa daya serap air menurun dari 18,3% hingga 5,5% dengan meningkatnya suhu pembakaran keramik stoneware BL1P dari 850 oC hingga 1200 oC. Dengan menggunakan pendekatan regresi linier diperoleh persamaan perubahan penyerapan air seperti pada persamaan (3) dengan koefisien determinasi R2= 0,96.
PA = -0,04T + 46,26 (3)
Penurunan penyerapan air tersebut mengindikasikan semakin berkurangnya voume pori-pori keramik sebagai akibat peningkatan suhu pembakaran.
Kuat lentur keramik diukur dengan stress maksimum yang mampu ditahan oleh keramik tersebut. Stress maksimum yang mampu ditahannya didefinisikan sebagai besar stress sesaat keramik sebelum patah. Pada metode three point bending patah terjadi pada bagian tengah dari balok uji [13]. Gambar 2 memperlihatkan perubahan kuat lentur terhadap suhu bakar, tampak bahwa peningkatan suhu pembakaran keramik stoneware BL1P dari 850 oC sampai dengan 1200 oC mengakibatkan peningkatan kuat lentur keramik dari 11,6 kg/cm2 hingga 19,8 kg/cm2. Dengan pendekatan regresi linier diperoleh persamaan perubahan kuat lentur sebagai fungsi temperatur seperti dinyatakan oleh persamaan (4) dengan kefisien determinasi R2 = 0,96.
σ = 0,02T - 8,66 (4)
Dengan peningkatan suhu bakar keramik stoneware BL1P dari 850 oC hingga 1200 oC terjadi penyempitan dan pengurangan jumlah pori-pori keramik yang mana mengakibatkan keramik menjadi semakin padat sehingga kuat lenturnya meningkat.
Suhu, T (oC)
Gambar 2.Grafik kuat lentur terhadap suhu bakar. Garis putus-putus adalah hasil fitting regresi linier.
Dari uraian di atas dapat disimpulkan bahwa peningkatan suhu bakar dalam proses pembuatan keramik stoneware BL1P dari 850 oC hingga 1200 oC berdampak terhadap penyeranan air dan kuat lenturnya. Dalam hal ini, pembakaran dari 850 oC hingga 1200 oC menurunkan daya serap airnya dari 18,3% hingga 5,5% dan meningkatkan kuat lenturnya dari 11,6 kg/cm2 hingga 19,8 kg/cm2.
Ucapan Terima Kasih
Banyak terima kasih kami ucapkan kepada Unit Pelaksana Teknis (UPT) Laboratorium Badan Pengkajian dan Penerapan Teknologi (BPPT) – Balai Teknologi Industri Kreatif Keramik (BTIKK) atas fasilitas, bahan baku yang telah diberikan serta bimbingannya selama penelitian.
Pustaka
-
[1] W.G. Lawrence and R.R. West, Ceramics Science for Potter, Pennsylvania: Chilton Book Company, 1982.
-
[2] T. Oishi, Ceramics Body, Gifu Prefecture Ceramics Research Institute Nagoya, International Training Center. Japan International Cooperation Agency, 1986.
-
[3] R. Behrens, Glaze Project, a Formula of Leadless Glazes, A Ceramics Monthly Magazine Handbook, Ohio: Profesional Publications, Inc., 1993.
-
[4] J.C. Miller and J.N. Miller, Statistics for Analytical Chemistry, Ellis Horwod Limited, New York,1998.
-
[5] Supomo, Karakterisasi dan Pengendalian Bahan Mentah Keramik, Diklat Quality Control Supervisor Industri Keramik Saniter dan Tableware, Bandung: BBIK, 1998.
-
[6] Nelson and C. Glen, Ceramics a Potterr’s Handbook, New York: John Wiley and Sons, 1986.
-
[7] B. Alexander, Panduan Praktis Kamus Keramik Untuk Praktisi, Perajin dan Industri, Milenia Populer, Jakarta: Australia – Indonesia, 2001.
-
[8] B. Mason and B.M. Carleton, Principles of Geochemistry, New York: John Wiley & Sons, 1982.
-
[9] K.N. Sundari, Makalah Ilmiah Pengkajian Industri, Deputi Teknologi Industri Rancang Bangunan & Rekayasa Badan Pengkajian dan Penerapan Teknologi. Denpasar, Bali, 2011.
-
[10] A.W. Vieira, M.D.M Innocentini, E. Mendes, et al., Comparison of Methods for Determining the Water Absorption of Glazed Porcelain Stoneware Ceramic Tiles, Material Research, 2017, pp. 1-2.
-
[11] C.B. Carter and M.G. Norton, Ceramic Materials Science and Engineering, Springer, 2013, pp. 305.
-
[12] D.A. Rozo, J.S. Molina and J.F. Gelves, Influence of raw materials and forming technique in the manufacture of stoneware ceramic, Ingeniería y competitividad, 2017, pp 93-105.
-
[13] L.R.S. Conserva, F.G. Melchiades, S. Nastri, et al., Pyroplastic Deformation of Porcelain Stoneware. In: Wet vs Dry Processing, Elsevier, 2016, pp. 3.
28
Discussion and feedback