Analisis Sistem Produksi Ikan Tuna Loin Segar Menggunakan Konsep Lean Thinking (Studi Kasus Di Cv. Kyu Karya Abadi)
on
ANALISIS SISTEM PRODUKSI IKAN TUNA LOIN SEGAR MENGGUNAKAN KONSEP LEAN THINKING
(STUDI KASUS DI CV. KYU KARYA ABADI)
I Putu Agus Amijaya1, I Wayan Widia2, I G.N. Apriadi Aviantara2 Email: gus_amy16@yahoo.co.id
ABSTRAK
Penelitian ini bertujuan untuk menganalisis sistem produksi ikan tuna loin segar menggunakan konsep Lean Thinking. Fokus dari analisis sistem produksi menggunakan konsep lean adalah mengurangi waktu tunggu dan mengurangi pemborosan sehingga pada akhirnya akan meningkatkan produktifitas. Hasil penelitian menunjukkan bahwa, ditemukan rata-rata waktu satu siklus produksi tuna loin segar di CV. Kyu Karya Abadi yaitu mencapai 299 menit, dengan distribusi 67 menit dihabiskan dari aktivitas-aktivitas value added dan sisanya 232 menit dihabiskan dari aktivitas-aktivitas non value added. Berdasarkan pengamatan terhadap tujuh jenis pemborosan, ditemukan terdapat satu jenis pemborosan yang terjadi di CV. Kyu Karya Abadi yaitu dikarenakan adanya produk cacat. Selain itu, pemborosan lainnya pada proses produksi di CV. Kyu Karya Abadi menggunakan process activity mapping terjadi oleh adanya jarak ruang produksi utama dengan ruang penyimpanan yang kurang berdekatan. Masih belum efisiennya proses produksi tuna loin segar di CV. Kyu Karya Abadi perlu menjadi perhatian pihak perusahaan untuk meningkatkan produktifitas produksi. Dari hasil tersebut diatas, dapat diberikan rekomendasi agar perusahaan menekan supplier untuk mengirimkan barang dengan kualitas terbaik sehingga dapat menurunkan persentase cacat.
Kata kunci : sistem produksi, tuna loin, lean thinking
ABSTRACT
The aim of this study is to analyze the production system of fresh tuna loin using Lean Thinking concept. The focus of the analysis production system using the lean concept are to reduce the waste and waiting time that will ultimately increase productivity. The results of the research showed that, the average cycle time of the production of fresh tuna loin in CV. Kyu Karya Abadi reached 299 minutes, in which 67 minutes was spent on value added activities and the rest 232 minutes was spent on the activities of non-value added. Based on observation of the seven types of waste, found there was one type of waste occur in the CV. Kyu Karya Abadi which was due to the defective products. Moreover, waste of the production process according to the process mapping activity in CV. Kyu Karya Abadi occurred by the distance of the main production room with the storage room which is less contiguous. Since there was still inefficient in the production processes of fresh tuna loin in CV. Kyu Karya Abadi, it the attention of the company is needed to increase the productivity of the production. Based on those results, it can be recommended that the company should pressing the supplier to deliver the highest quality goods, therefore they can reduce the percentage of defective.
Keywords: production system, tuna loin, Lean thinking
PENDAHULUAN
Latar Belakang
Pangan merupakan kebutuhan dan hak dasar manusia. Penyediaan pangan tidak hanya menyangkut jumlahnya tetapi juga keamanannya. Aspek keamanan pangan sangat penting karena berkaitan erat dengan kesehatan masyarakat. Dalam perdagangan global, sering diterapkan standar keamanan pangan yang diakui secara internasional, sehingga mau tidak mau produsen pangan harus mampu melaksanakan sistem manajemen keamanan pangan untuk dapat bersaing di pasar global.
Ikan tuna (Thunnus Sp.) merupakan salah satu produk pangan hasil tangkapan laut yang memilki nilai ekonomis yang tinggi dan mampu menembus pasar internasional.Potensi ikan tuna di perairan Indonesia masih cukup besar. Hal ini ditunjukkan dengan volume produksi ikan tuna pada tahun 2007 yaitu sebesar 191.558 ton (DKP, 2008). Ikan tuna khususnya untuk di daerah Bali paling banyak di ekspor ke Jepang, Amerika, dan Eropa (Diskelkan Bali, 2012). Menurut data Dinas Kelautan dan Perikanan Provinsi Bali tahun 2012 ekspor tuna selama tahun 2007 sampai 2011 mencapai angka 269.914.099 USD. Di daerah Bali terdapat sentra-sentra agroindustri ikan dengan hasil tangkapan ikan tuna berjumlah 14 sentra yang tersebar diseluruh kabupaten, dengan sentra utama terdapat di Kabupaten Jembrana, Klungkung, Badung, dan Buleleng (BPS, 2012).
Hasil pemantauan dilapangan ditemukan bahwa CV. Kyu Karya Abadi merupakan salah satu perusahaan yang bergerak di bidang seafood supplier. Perusahaan ini berdiri pada tahun 1990. Namun seiring perjalanan perusahaan hingga saat ini belum memperlihatkan perkembangan yang signifikan. Hal ini dikarenakan proses pembuatan tuna loin segar di perusahaan tersebut tidak terlepas dari ketidakefisien dalam berproduksi. Permasalahan proses produksi yang terjadi di perusahaan ini dapat diatasi dengan suatu konsep bisnis yaitu Lean thinking. Lean Thinking merupakan suatu pendekatan yang sistematis terhadap pemborosan (waste) dalam berbagai proses secara terus-menerus (continuous) untuk mengoptimalkan value stream dengan menghilangkan segala bentuk pemborosan (waste) serta meningkatkan penambahan nilai (value added) produk agar dapat memberikan nilai tambah kepada pelanggan. Adapun tujuan dari penelitian ini adalah mengidentifikasi aktivitas-aktivitas yang bernilai tambah dan yang tidak bernilai tambah pada proses produksi ikan tuna loin segar di CV. Kyu Karya Abadi, dan identifikasi pemborosan yang terjadi dengan konsep tujuh jenis pemborosan dan process activity mapping.
METODE PENELITIAN
Tempat dan Waktu Penelitian
Penelitian ini dilakukan di supplier ikan di Singaraja tepatnya di Desa Les Kecamatan Tejakula Kabupaten Buleleng yang merupakan salah satu pemasok ikan tuna ke perusahaan CV. Kyu Karya Abadi dan di Perusahaan seafood supplier CV. Kyu Karya Abadi, Kelan, Tuban, Badung. Penelitian ini dilaksanakan pada bulan Oktober sampai Desember 2012.
Alat dan Bahan
Alat yang digunakan dalam penelitian ini adalah menggunakan timbangan, meteran dan stopwatch. Adapun bahan yang digunakan adalah ikan tuna sirip kuning (yellowfin) dari nelayan Made Maliastra. Berat ikan yang dipasok ke perusahaan CV. Kyu Karya Abadi berkisar antara 23-30 kg.
Pelaksanaan Penelitian
Analisis proses produksi menggunakan konsep Lean Thinking dimulai dengan melakukan observasi di perusahaan CV. Kyu Karya Abadi untuk mengetahui tahapan proses produksi dan observasi kondisi di supplier ikan Desa Les. Analisis proses produksi menggunakan konsep dasar Lean Thinking di CV. Kyu Karya Abadi di fokuskan pada waktu produksi. Waktu produksi sangat berpengaruh terhadap peluang terjadinya pemborosan. Perhitungan waktu produksi dimulai dari supplier mengirim ikan hingga ikan siap dikirim ke konsumen.
Value stream mapping (VSM) merupakan salah satu metode Lean Thinking yang digunakan untuk memvisualisasikan peta atau gambaran dari proses produksi. VSM digunakan sebagai langkah awal dalam mengenali, mengetahui pemborosan yang ditimbulkan dalam suatu proses produksi. Dalam pembuatan VSM terdapat dua aktivitas penting, yaitu value added dan non value added. Value added adalah aktivitas mengubah bentuk atau menambah fungsi dari suatu produk atau jasa sehingga memberikan nilai tambah pada produk atau jasa. Sedangkan non value added adalah aktivitas yang tidak merubah sesuatu, namun menimbulkan biaya dan tidak memberikan nilai tambah (George, 2002).
Setelah melakukan pemetaan, maka akan tergambar tentang proses produksi dari awal sampai akhir, sehingga dapat dengan mudah mengidentifikasi pemborosan yang terjadi dengan menggunakan konsep tujuh jenis pemborosan yang sesuai dengan teori Linker (2006) tentang tujuh pemborosan yang dipercaya bertanggung jawab dalam 95% biaya total dalam proses produksi. Maka dari itu, dilakukan perangkingan tujuh jenis pemborosan untuk memudahkan dalam memberikan saran perbaikan. Perangkingan tujuh jenis pemborosan ini dengan melakukan wawancara dengan pihak perusahaan tentang proses produksi selama tiga bulan terakhir, sehingga nantinya akan dengan mudah mengetahui pemborosan yang paling
berpengaruh dalam proses produksi di perusahaan. Jenis wawancara yang dilakukan adalah in-deph interview yang diberikan langsung kepada bagian produksi. Kriteria tinggi, sedang, atau rendahnya pemborosan ditentukan oleh bagian produksi melalui wawancara.
Setelah melakukan perangkingan tujuh jenis pemborosan maka dilanjutkan dengan menganalisis aliran nilai dengan menggunakan VALSAT. VALSAT (Value Stream Analysis Tools) merupakan alat yang dikembangkan untuk mempermudah pemahaman terhadap aliran nilai, mempermudah untuk membuat perbaikan berkenaan dengan pemborosan (Hines, 2004). Terdapat tujuh alat dari VALSAT yang bermanfaat untuk memetakan pemborosan, namun pada penelitian ini alat yang dipilih adalah process activity mapping.
Setelah diketahui semua jenis pemborosan yang terjadi maka langkah selanjutnya adalah dengan memberikan rekomendasi perbaikan proses produksi. Rekomendasi yang diberikan dapat perusahana pilah satu persatu dan ditentukan pada stasiun kerja mana yang menjadi prioritas perbaikan. Perbaikan haruslah perusahaan lakukan untuk lebih mengefektifkan proses produksi karena mengacu pada prinsip dari Lean thinking adalah perbaikan terus-menerus untuk meningkatkan produktifitas.
Diagram alir pelaksanaan penelitian
Gambar 1. Diagram alir pelaksanaan penelitian 4
Variabel yang diamati
Variabel yang diamati pada penelitian ini adalah :
-
1. Jenis proses pada setiap stasiun kerja yang dinyatakan dalam nama proses. Untuk menentukan nama dari setiap tahapan proses adalah dengan observasi langsung ke perusahaan dengan melihat langsung proses produksi.
-
2. Waktu proses pada setiap stasiun kerja yang dinyatakan dalam menit (m). Perhitungan waktu di setiap stasiun kerja ditentukan dengan menghitung waktu pada saat produk diserahkan kestasiun kerja dan di serahkan kembali kestasiun kerja berikutnya. Perhitungan waktu disetiap stasiun kerja dengan menggunakan stopwatch.
-
3. Jumlah personalia pada setiap stasiun kerja yang dinyatakan dalam orang. Jumlah personalia dihitung berdasarkan observasi langsung di perusahaan.
-
4. Jarak pada setiap stasiun kerja yang berdekatan yang dinyatakan dengan meter (mtr). Perhitungan jarak disetiap stasiun kerja yang berdekatan adalah dengan menggunakan meteran.
-
5. Jenis peralatan atau mesin yang digunakan setiap stasiun kerja yang dinyatakan dengan nama alat atau mesin. Identifikasi alat ataupun mesin yang digunakan adalah dengan obeservasi langsung diperusahaan.
HASIL DAN PEMBAHASAN
Hasil Analisis Proses Produksi Ikan Tuna Loin Segar Menggunakan Konsep Dasar Lean Thinking
Produk yang aman saja tidaklah cukup bersaing di dunia bisnis jaminan mutu juga merupakan salah satu faktor penentu daya saing produk yang harus selalu ditingkatkan. Low cost, sangatlah penting dalam usaha bertahan dalam persaingan bisnis saat ini. Low cost dapat diperoleh dengan berbagai macam cara, salah satunya dengan menekan serendah mungkin biaya penyimpanan, waktu produksi yang pendek dan sebagainya yang dapat menekan biaya produksi (Farisi, 2010).
Value stream mapping adalah suatu alat dari Lean Thinking yang sudah biasa digunakan oleh perusahaan untuk mengurangi segala aktivitas yang tidak bernilai tambah (Non Value Added). Penggambaran aliran nilai yang diaplikasikan di perusahaan CV. Kyu Karya Abadi dari tiga kali pemantauan dapat dilihat pada Gambar 1. dibawah ini :
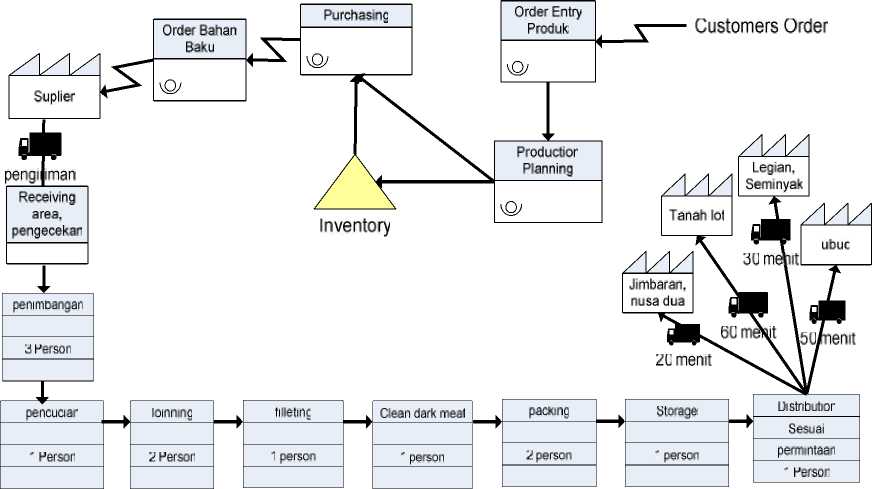
pengiriman pengecekan penimbangan pencucian Loinning Filleting Cleandarkmeat
Packing
V/A I ime =
Non V/A =

= 63 menit
= 18« menit
Value Added Time As a % OfTotaI Iimcin Plant- 63 minutes / 189 minutes-33,33 % (Pemantauan I)
pengiriman pengecekan penimbangan pencucian Loinning Filleting Cleandarkmeat Packing

Value Added Γιmc As a % of Total Γιmc in Plant - 57 minutes /237 minutes - 24,05 % (Pemantauan II)
= b / menit
= 23/ menit
1b menιt
pengiriman pengecekan penimbangan pencucian Loinning Filleting Cleandarkmeat Packing
31 16 16
me∩∣t men∣t menιt
v/A Iime =
Non v∕A =

Value Added Γιme As a % of I otal l ime in Plant - 80 minutes /272 minutes - 29,41 % (Pemantauan III)
= BU menιt
= 2/2 menιt
Gambar 2. Value Stream Mapping Proses Produksi Ikan Tuna Loin Segar
Berdasarkan Gambar 1. diatas data menunjukkan rata-rata waktu dari satu siklus produksi tuna loin segar di perusahaan ini yaitu mencapai 299 menit, dengan distribusi waktu 67 menit dihabiskan dari aktivitas-aktivitas value added. Distribusi waktu 67 menit tersebut paling banyak dihabiskan untuk proses loinning dengan rata-rata waktu 28 menit, karena proses pembelahan tuna menjadi empat bagian inilah yang disebut dengan loin sehingga tahap ini merupakan proses kunci pembuatan tuna loin.
Sisa waktu 232 menit dihabiskan dari aktivitas-aktivitas non value added. Pengiriman menjadi aktivitas yang tidak bernilai tambah dengan menghabiskan waktu dengan rata-rata 210 menit. Hal ini disebabkan karena jarak supplier yang jauh dengan topografi yang berbukit dan 6
melintasi daerah perkotaan yang pada pagi hari selalu mengalami kemacetan. Masih banyaknya aktivitas yang non value added perlu mendapat perhatian dari pihak perusahaan agar nantinya mampu mengurangi aktivitas tersebut.
Hasil wawancara untuk mengetahui tujuh jenis pemborosan produksi ikan tuna loin segar selama tiga bulan terakhir dapat dilihat pada Tabel 1. Tabel Memperlihatkan data bahwa cacat termasuk pemborosan yang tinggi karena dari tiga bulan terakhir produk cacat berjumlah 120 kg. Transportasi dan proses yang tidak tepat termasuk pemborosan kategori sedang karena berdasarkan hasil wawancara masih banyaknya produk kembali akibat produk rusak karena daging putih atau daging seperti bubur, dan kemudian proses yang tidak tepat disebabkan karena personalia yang bekerja teledor sehingga mengakibatkan produk mengalami kerusakan.
Tabel 1. Ranking Seven Waste
Aktivitas |
Tinggi |
Sedang |
Rendah |
Cacat |
V | ||
Transportasi |
V | ||
Proses yang tidak tepat |
V | ||
Pergerakan yang tidak perlu |
V | ||
Persediaan |
V | ||
Produksi berlebih |
V | ||
Menunggu |
V |
Untuk pergerakan yang tidak perlu kategori rendah karena proses produksi berjalan dalam satu tempat. Kemudian persediaan termasuk rendah karena setiap harinya perusahaan hanya menyiapkan cadangan whole tuna dua sampai empat ekor dan untuk produk jadi 15 kg. Selama tiga bulan terakhir hampir tidak ada produksi berlebih. Menunggu pasokan ikan dari suplier dalam tiga bulan terakhir proses produksi hanya tiga kali saja sehingga menunggu tergolong pemborosan kategori rendah.
Dari perangkingan tujuh pemborosan ini untuk pemborosan yang paling tinggi yaitu produk cacat saran yang dapat diberikan adalah dengan menekan supplier untuk mengirimkan ikan tuna dengan kualitas yang terbaik sehingga nantinya dapat menurunkan persentase cacat dan juga dapat mengurangi transportasi dan proses kerja ulang (rework) yang tidak perlu.
Data pada Tabel 2, 3 dan 4, memperlihatkan process activity mapping yang terjadi di perusahaan CV. Kyu Karya Abadi. Tabel menampilkan data bahwa aktivitas penyimpanan merupakan pemborosan yang paling berpengaruh, karena dari jarak ruang utama produksi ke tempat penyimpanan memerlukan pergerakan yang cukup jauh dibandingkan proses lainnya yaitu ± 10 meter.
Dari penjelasan diatas dan analisa dari proses produksi tuna loin segar maka penulis memberikan rekomendasi yang nantinya diharapakan dapat membantu dalam proses produksi agar dapat berjalan efektif.
Rekomendasi perbaikan proses produksi ikan tuna loin di perusahaan CV. Kyu Karya Abadi dapat dilihat pada Tabel 5. dibawah ini:
Tabel 5. Rekomendasi perbaikan proses produksi
Pemborosan |
Akar masalah |
Rekomendasi perbaikan |
Cacat |
Kualitas material yang kurang bagus |
Menekan supplier untuk mengirimkan barang dengan kualitas terbaik sehingga nantinya dapat menurunkan persentase cacat. |
Proses yang tidak tepat |
Perbedaan metode kerja antar operator |
Pemasangan SOP untuk setiap aktivitas pada setiap stasiun kerja |
Transportasi |
Pengiriman ulang karena produk rusak |
Inspeksi produk yang akan dikirim. |
Menunggu |
Produk menunggu yang terlalu lama. |
Harus adanya penstandaran operasi kerja antar operator. |
Pergerakan yang tidak perlu |
Letak peralatan yang berjauhan dari area kerja. |
Peletakan tool yang digunakan operator disesuaikan dengan kebutuhan proses produksi |
Persediaan |
Penumpukan persediaan yang tidak menetap |
Melakukan perbaikan penjadwalan proses produksi. |
Produksi berlebih |
Tidak adanya permintaan yang tetap setiap harinya. |
Harus adanya peramalan produksi yang pasti. |
KESIMPULAN DAN SARAN
Kesimpulan
Berdasarkan hasil penelitian analisis sistem produksi ikan tuna loin menggunakan konsep Lean Thinking studi kasus di CV. Kyu Karya Abadi dapat ditarik kesimpulan bahwa
-
1. Penelitian Lean Thinking yang terkait dengan efisiensi produksi ditemukan bahwa rata-rata waktu satu siklus produksi tuna loin segar di CV. Kyu Karya Abadi yaitu mencapai 299 menit, dengan distribusi 67 menit dihabiskan dari aktivitas-aktivitas value added dan sisanya 232 menit dihabiskan dari aktivitas-aktivitas non value added.
-
2. Ranking tertinggi tujuh jenis pemborosan pada proses produksi ikan tuna loin segar selama tiga bulan terakhir adalah produk cacat mencapai 120 kg.
-
3. Berdasarkan process activity mapping pemborosan proses produksi di CV. Kyu Karya Abadi terjadi oleh adanya jarak ruang produksi utama dengan ruang penyimpanan yang kurang berdekatan.
Saran
Perlunya adanya perbaikan terus-menerus dari setiap stasiun kerja agar non value addednya dapat dikurangi atau dihilangkan. Perubahan lantai produksi perlu dilakukan secara bertahap, untuk lebih meningkatkan produktifitas.
DAFTAR PUSTAKA
Biro Pusat Statistik (BPS) Provinsi Bali. 2012. Sentra Agroindustri Ikan Tuna Tahun 2012.
Diskelkan, 2007. Frekuensi Ekspor Perikanan Bali 2007-2011. Provinsi Bali
[DKP] Departemen Kelautan dan Perikanan. 2008. Statistik Ekspor Hasil Perikanan 2007. Jakarta: DKP.
Farisi, M Iqbal. 2010. Peningkatan Produktifitas Dengan Menggunakan Metode Lean Thinking (Studi Kasus) Di CV. Sinar Mulia Sejahtera. Skripsi. Jurusan Teknik Industri. Fakultas Teknologi Industri. Universitas Pembangunan Nasional “Veteran” Jawa Timur. Jawa Timur.
George, ML. 2002. Lean Six Sigma. New York: Mc GrawHill.
Hines, P.2004. Value Stream Mapping : Theory and Case. Cardiff University.
Linker, Jeffrey K & Meier David.2006. Toyota Way Fieldbook. The McGraw-Hill Companies.Inc. New York. United States.
10
Discussion and feedback